Electrically Conductive Rubber Profiles with Excellent Resilience, and Sealing Capabilities
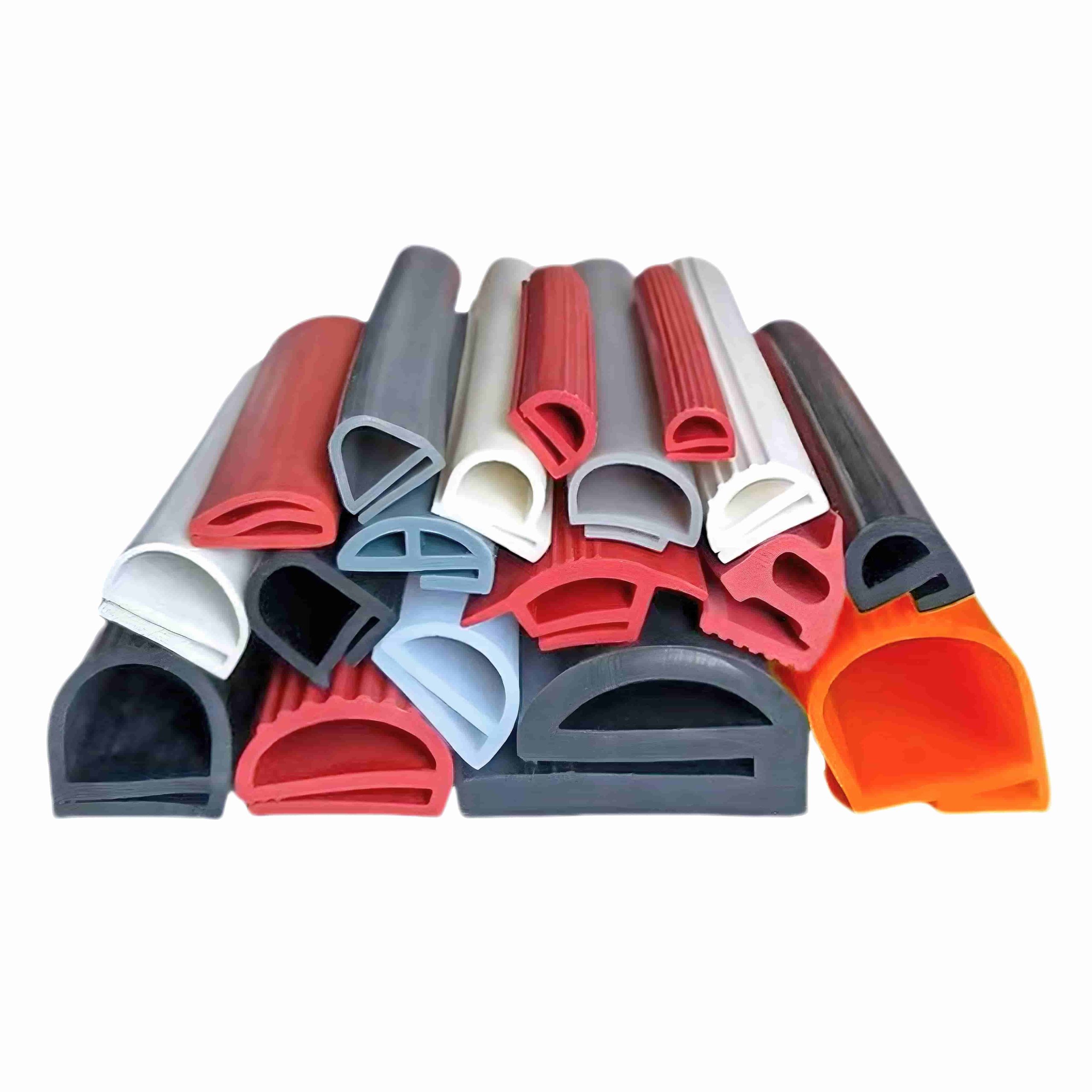
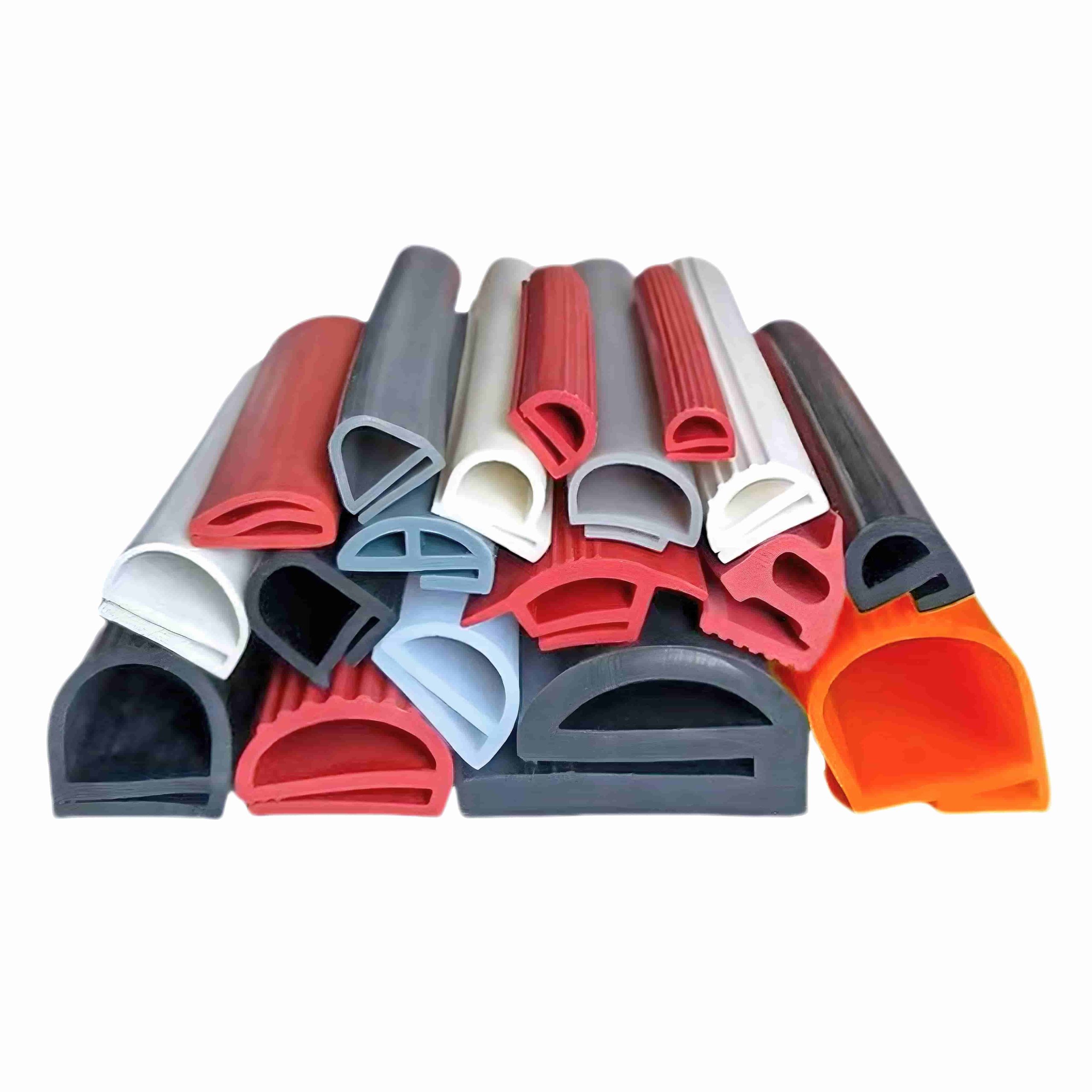
Electrically conductive rubber profiles represent a unique intersection of material science and engineering, combining the flexibility and sealing properties of traditional rubber with the ability to conduct electricity. This makes them essential in various applications, particularly in sectors where electrical performance and mechanical reliability are critical. These specialized components are manufactured by incorporating conductive fillers, such as carbon black or metal particles, into rubber polymers.
Electrically conductive rubber profiles represent a unique intersection of material science and engineering, combining the flexibility and sealing properties of traditional rubber with the ability to conduct electricity. This makes them essential in various applications, particularly in sectors where electrical performance and mechanical reliability are critical. These specialized components are manufactured by incorporating conductive fillers, such as carbon black or metal particles, into rubber polymers. This article explores the features, benefits, applications, and manufacturing processes of electrically conductive rubber profiles, shedding light on their importance in modern industrial settings.
Table of Contents
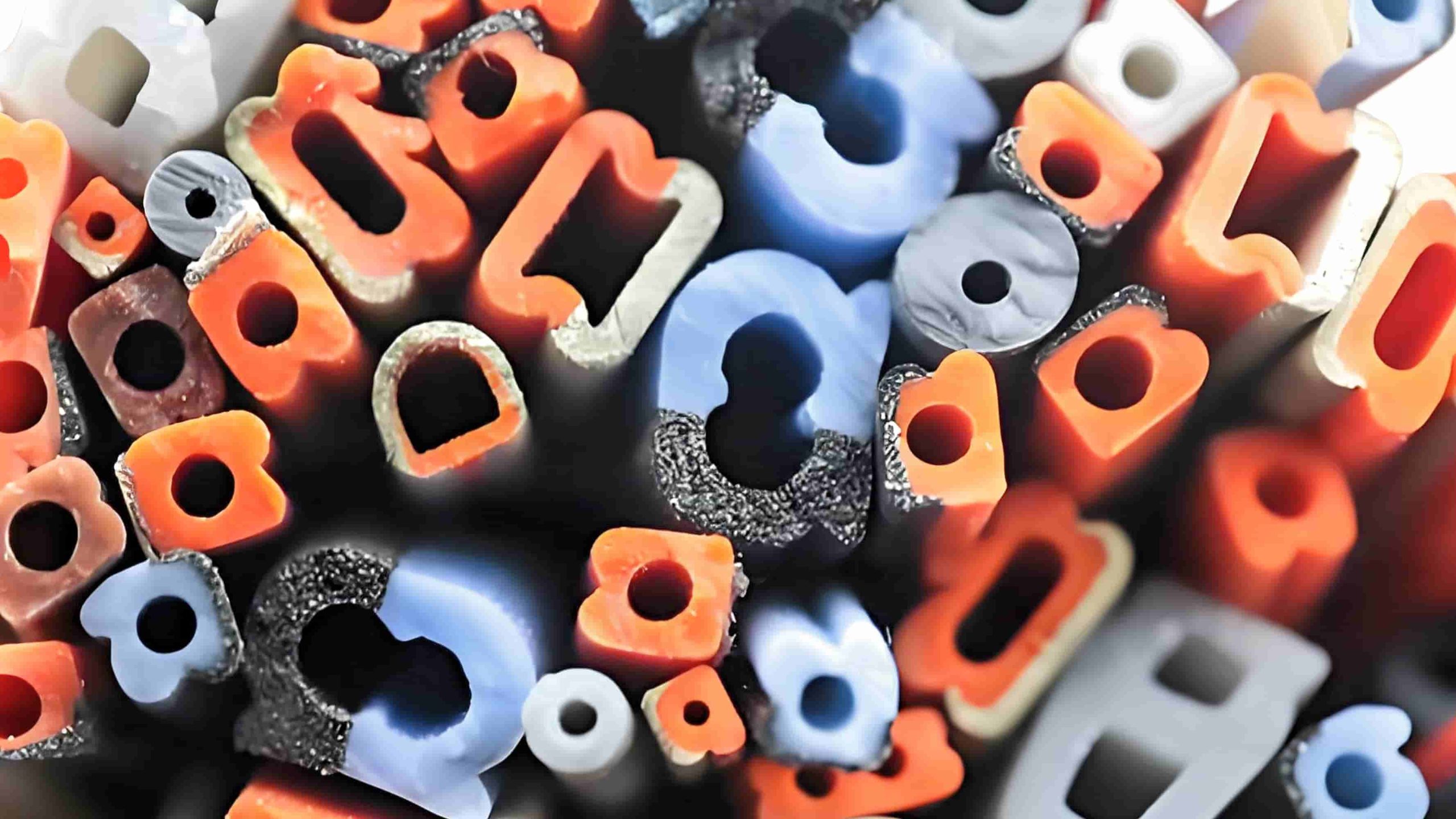
Electrically Conductive Rubber Profiles
What Are Electrically Conductive Rubber Profiles?
Electrically conductive rubber profiles are rubber components engineered to facilitate the flow of electrical current while retaining the inherent advantages of rubber, such as flexibility, resilience, and sealing capabilities. They are particularly valuable in environments where both electrical and mechanical performance are paramount.
Composition and Materials
The primary materials used in electrically conductive rubber profiles include:
- Rubber Polymers: The base material that provides flexibility and durability. Commonly used types include natural rubber, silicone rubber, and neoprene.
- Conductive Fillers: These materials are mixed with the rubber polymers to impart electrical conductivity. Common fillers include:
- Carbon Black: A widely used filler that enhances conductivity while maintaining rubber properties.
- Metal Particles: Materials such as copper, aluminum, or silver can be used for higher conductivity levels.
Key Features and Benefits
1. Electrical Conductivity
One of the most significant features of electrically conductive rubber profiles is their ability to conduct electricity. This conductivity can be tailored to meet specific requirements, making these profiles suitable for various applications. The conductivity is achieved by carefully controlling the concentration and type of conductive fillers used in the rubber matrix.
2. Flexibility and Sealing Properties
Despite their electrical conductivity, these rubber profiles maintain the inherent flexibility and resilience characteristic of rubber materials. This makes them ideal for applications that require not only electrical functionality but also effective sealing against environmental factors such as dust, moisture, and chemicals.
3. Versatility
Electrically conductive rubber profiles can be designed for a broad range of industrial applications. Their adaptability allows them to be used in diverse sectors, including automotive, electronics, aerospace, and manufacturing.
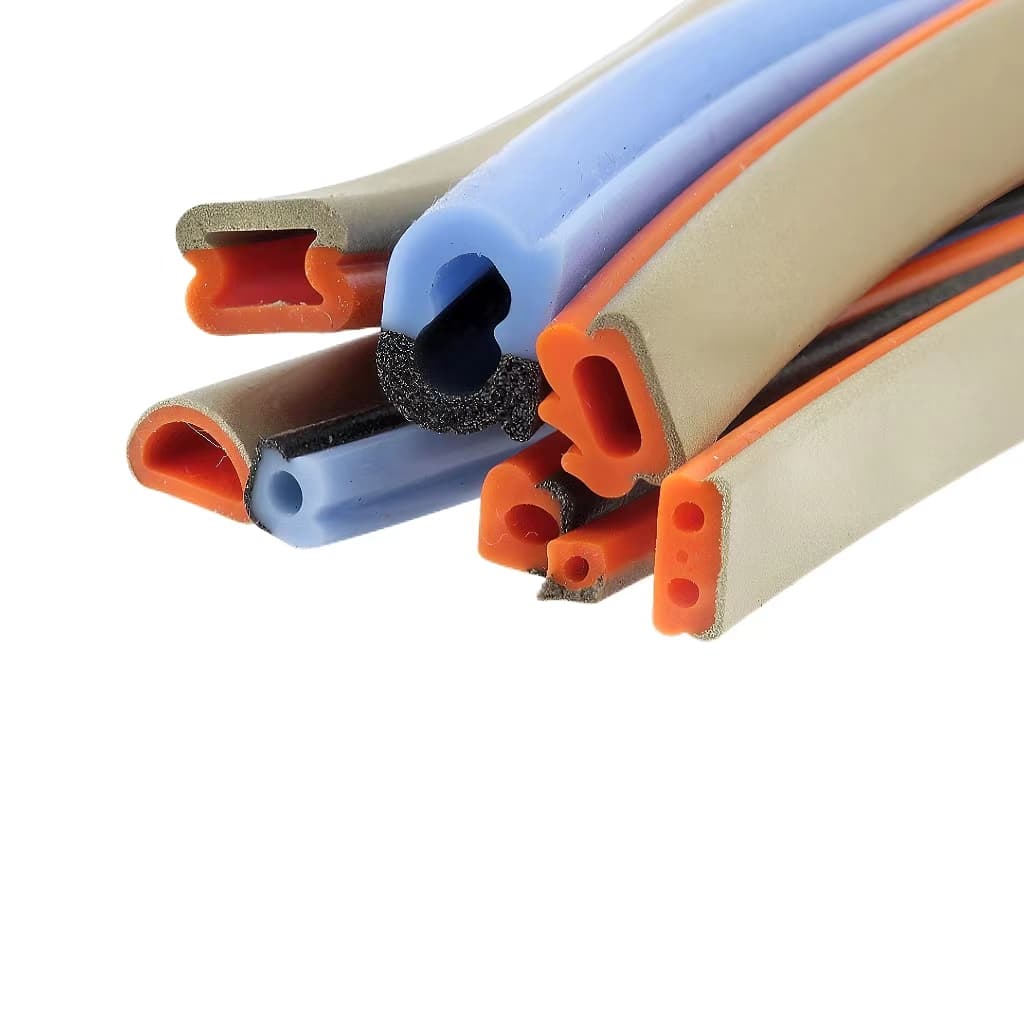
Applications of Electrically Conductive Rubber Profiles
The versatility of electrically conductive rubber profiles allows for their use in numerous applications, including:
1. EMI/RFI Shielding
Electrically conductive rubber profiles are widely used for electromagnetic interference (EMI) and radio-frequency interference (RFI) shielding. They prevent the transmission of electromagnetic waves, protecting sensitive electronic components from interference that could disrupt their functionality. This shielding is essential in various electronic devices and systems, ensuring reliable operation.
2. Static Dissipation
These profiles also play a critical role in static dissipation, helping to dissipate static charges and prevent electrostatic discharge (ESD). ESD can damage electronic components, making electrically conductive rubber profiles vital in environments such as electronics manufacturing and assembly, where sensitive devices are handled.
3. Electrical Connectors and Contacts
Electrically conductive rubber profiles ensure reliable electrical connections in various applications. They provide a compliant interface that accommodates variations in mating surfaces, which is crucial for maintaining effective contact and minimizing resistance in electrical circuits. This feature is particularly valuable in automotive and industrial machinery.
4. Heating Elements
In some applications, electrically conductive rubber profiles serve as heating elements. When an electrical current passes through them, they generate heat, making them suitable for use in heated mats, automotive seat warmers, and medical devices. Their flexibility allows them to conform to various shapes, enhancing their usability in different products.
5. Industrial Equipment Seals
In industrial settings, electrically conductive rubber profiles can be used as seals for equipment, providing both sealing capabilities and electrical conductivity. This dual functionality is particularly advantageous in environments where equipment is exposed to harsh conditions, such as moisture or chemicals, while also requiring grounding or static control.
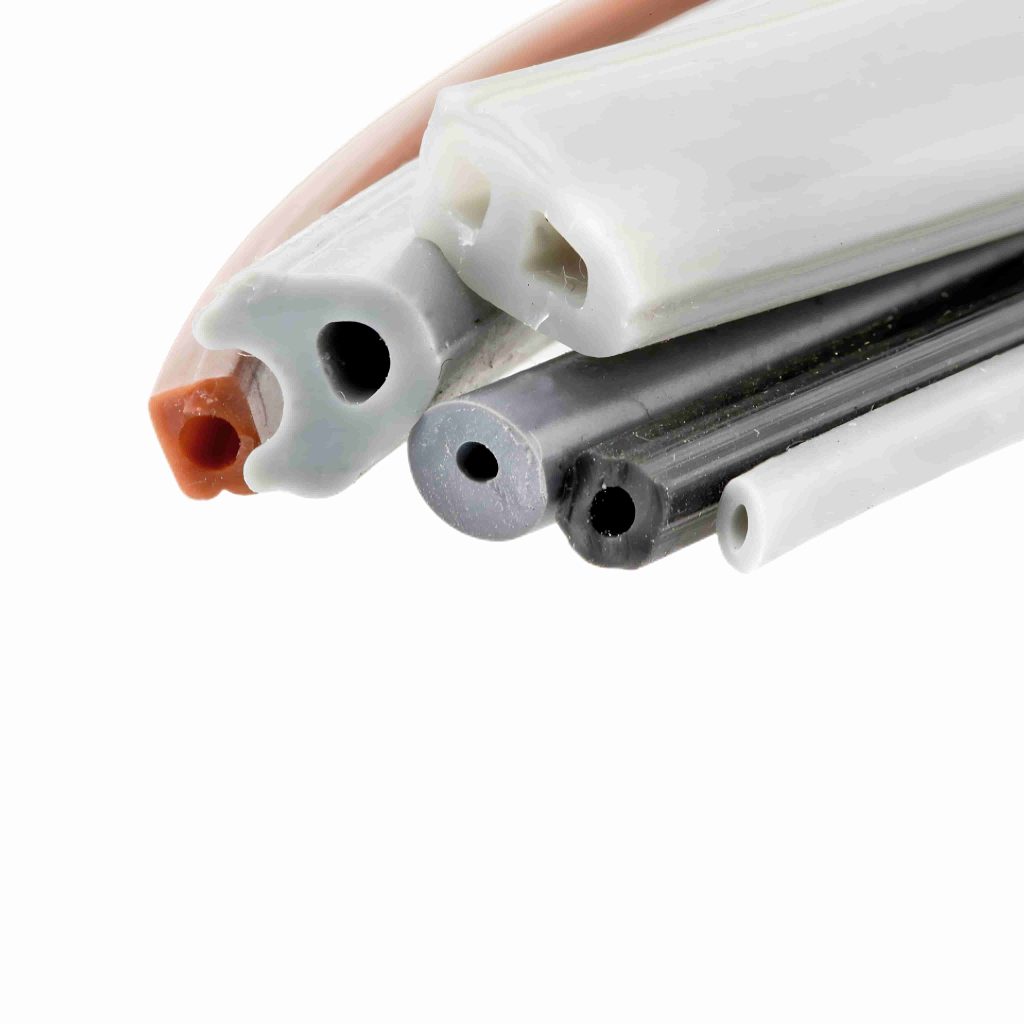
Manufacturing Process of Electrically Conductive Rubber Profiles
The production of electrically conductive rubber profiles involves several steps:
- Compounding: The first step is combining rubber polymers with conductive fillers. The specific formulation depends on the desired electrical properties and the application requirements. This process often involves mixing the rubber with the fillers in a controlled environment to ensure a uniform distribution.
- Molding or Extrusion: Once the compound is prepared, it is shaped into profiles using molding or extrusion techniques. In molding, the compound is placed in a mold and heated to cure the rubber, while extrusion involves forcing the compound through a die to create continuous profiles.
- Curing: The shaped rubber is cured to enhance its mechanical properties and set its shape. Curing can involve heat, pressure, or a combination of both, depending on the specific rubber formulation used.
- Quality Control: Throughout the manufacturing process, quality control measures are implemented to ensure that the final product meets the required specifications for electrical conductivity, mechanical strength, and other performance characteristics.
Conclusion
In conclusion, electrically conductive rubber profiles are an essential component in today’s industrial landscape, merging the advantages of rubber with the critical requirement for electrical conductivity. Their unique properties and versatility make them indispensable in applications that demand reliable sealing and electrical performance. As technology advances and industries expand, the significance of these profiles is set to increase, paving the way for innovative solutions that meet the complex demands of modern applications.
By understanding the features, benefits, and applications of electrically conductive rubber profiles, engineers and manufacturers can harness their potential to develop products that not only perform effectively but also contribute to the efficiency and reliability of various systems and devices.
You May Also Like
-
Handa Canted Coil Springs
EMI Shielding Springs
EMI shielding canted coil springs, also known as canted coil springs, are innovative components designed to provide effective electromagnetic interference (EMI) and radio frequency interference (RFI) shielding while also serving as mechanical springs. These springs are characterized by their unique canted coil design, which enables them to provide multiple points of contact for superior EMI shielding, mechanical latching, and electrical conductivity. What Are EMI Shielding Canted Coil Springs?Applications of EMI Shielding Canted Coil SpringsMaterials and Construction of EMI Shielding Canted Coil SpringsBenefits of EMI Shielding Canted Coil SpringsStandards Compliance for EMI Shielding Canted Coil SpringsConsiderations When Using EMI Shielding Canted Coil SpringsConclusion https://www.handashielding.com/contact-us.html What Are EMI Shielding Canted Coil Springs? EMI shielding springs are specialized springs that offer both mechanical and electromagnetic shielding capabilities. Their canted coil design features coils arranged at an angle, which creates multiple points of contact when compressed. This allows the spring to function as both a mechanical component and a highly effective EMI/RFI shield. Electromagnetic interference is a significant concern in modern electronic devices, where external or internal EMI can disrupt signals and affect performance. EMI shielding springs are designed to protect sensitive electronic components from EMI and RFI while also providing mechanical and electrical......
-
EMI/EMC Shielding | RFI Shielding | EMI Gaskets
Fingerstrips
Electromagnetic interference (EMI) can create significant issues for electronic devices and systems, leading to decreased performance, potential malfunction, or even failure. This is where stick-on mounting fingerstrips come in as an essential EMI shielding solution, especially for low-profile, bidirectional applications. These adhesive-backed beryllium-copper strips are designed to be easily installed without the need for specialized tools, providing an efficient and cost-effective way to shield electronics from EMI. In this article, we will explore the features, applications, benefits, and importance of stick-on mounting fingerstrips in EMI shielding. Whether you are working in telecommunications, computer hardware, or any industry where electromagnetic interference poses a risk, stick-on fingerstrips can provide a practical solution. Key Features of Stick-on Mounting Fingerstrips1. Adhesive Backing2. Low-Profile Design3. Beryllium-Copper Construction4. Bi-directional Sealing5. Adjustable SizeApplications of Stick-on Mounting Fingerstrips1. Telecommunications Equipment2. Narrow Electronics Enclosures3. General EMI Shielding Applications4. Computer HardwareBenefits of Stick-on Mounting Fingerstrips1. Easy Installation2. Consistent Sealing3. Flexibility4. Durability5. VersatilityHow Stick-on Mounting Fingerstrips Help with EMI ShieldingMinimizing Electromagnetic InterferenceMaintaining Performance in High-EMI EnvironmentsEnhancing System ReliabilityConclusion Stick-on Mounting Fingerstrips https://www.handashielding.com/contact-us.html Key Features of Stick-on Mounting Fingerstrips When choosing an EMI shielding solution, it’s important to focus on certain key features to ensure that the product you select meets your......
-
EMI/EMC Shielding | RFI Shielding | EMI Gaskets
Fingerstrips
Snap-on mounting fingerstrips are highly effective Electromagnetic Interference (EMI) shielding components used in various electronic enclosures and assemblies to ensure electromagnetic integrity and prevent radio frequency interference (RFI). With the advancement of electronic systems, EMI shielding has become crucial to maintaining the functionality and performance of sensitive electronic devices. Snap-on mounting fingerstrips are designed for easy installation, flexibility, and efficient shielding, making them a popular choice across numerous industries, including telecommunications, military, aerospace, automotive, and consumer electronics. This article will provide a detailed exploration of snap-on mounting fingerstrips, focusing on their key features, materials, installation methods, applications, and benefits. Additionally, we will explore why snap-on mounting fingerstrips are an essential component in modern electronics and how they meet the demands of EMI/RFI shielding requirements. https://www.handashielding.com/contact-us.html What are Snap-On Mounting Fingerstrips?Key Features of Snap-On Mounting FingerstripsTypes of Snap-On Mounting FingerstripsInstallation Method of Snap-On Mounting FingerstripsCommon Applications of Snap-On Mounting FingerstripsMaterial Options for Snap-On Mounting FingerstripsBenefits of Using Snap-On Mounting FingerstripsConclusion: Snap-On Mounting Fingerstrips in EMI Shielding What are Snap-On Mounting Fingerstrips? Snap-on mounting fingerstrips are flexible EMI shielding gaskets made from materials such as beryllium copper, phosphor bronze, or other conductive alloys. They are specifically designed to create a secure electrical......
-
EMI tapes, EMC foils, conductive textiles & half conductive non-woven
Copper foil tape
Conductive copper foil tape is a highly versatile and indispensable material widely used in industries ranging from electronics to automotive. Its unique combination of electrical conductivity and adhesive properties allows it to serve as an efficient solution for various applications, particularly in shielding, grounding, and conducting electricity between components. This comprehensive guide explores the key features, applications, types, properties, performance, and industries in which conductive copper foil tape plays a crucial role. Key Features of Conductive Copper Foil TapeTypes of Conductive Copper Foil TapeApplications of Conductive Copper Foil TapeProperties and Performance of Conductive Copper Foil TapeConsiderations for Choosing Conductive Copper Foil Tape Conductive Copper Foil Tape Key Features of Conductive Copper Foil Tape Conductive copper foil tape is designed to meet the high demands of modern electronic and industrial applications. Below are its defining features: 1. Electrical Conductivity One of the primary advantages of conductive copper foil tape is its excellent electrical conductivity. Copper, being one of the most conductive materials, allows electrical signals to flow efficiently across surfaces. This makes the tape an essential component in applications that require grounding, EMI (Electromagnetic Interference) shielding, or electrical signal transmission between two or more components. 2. Chemical Resistance Conductive copper foil......
-
EMI tapes, EMC foils, conductive textiles & half conductive non-woven
Conductive aluminium tape
Electrical conductivity aluminum foil tape is a versatile and essential material in various industries, particularly in electronics, electrical engineering, and construction. This article delves deep into the properties, applications, benefits, and selection criteria for electrical conductivity aluminum foil tape, focusing on why it is indispensable for ensuring electrical continuity, shielding, and grounding. https://www.handashielding.com/contact-us.html What is Electrical Conductivity Aluminum Foil Tape?Key Properties of Electrical Conductivity Aluminum Foil TapeApplications of Electrical Conductivity Aluminum Foil TapeBenefits of Using Electrical Conductivity Aluminum Foil TapeSelection Criteria for Electrical Conductivity Aluminum Foil TapeConclusion What is Electrical Conductivity Aluminum Foil Tape? Electrical conductivity aluminum foil tape is a specialized adhesive tape made from thin aluminum foil coated with an electrically conductive adhesive. This tape is designed to offer excellent conductivity across its surface and through its adhesive, making it ideal for applications requiring reliable electrical connections and shielding. The aluminum foil provides a conductive surface, while the adhesive ensures that the tape adheres firmly to various substrates while maintaining electrical conductivity. Key Properties of Electrical Conductivity Aluminum Foil Tape 1. Electrical Conductivity The primary feature of aluminum foil tape is its excellent electrical conductivity. Both the aluminum foil and the conductive adhesive are designed to allow current......