Electrically conductive foam for a wide range of applications
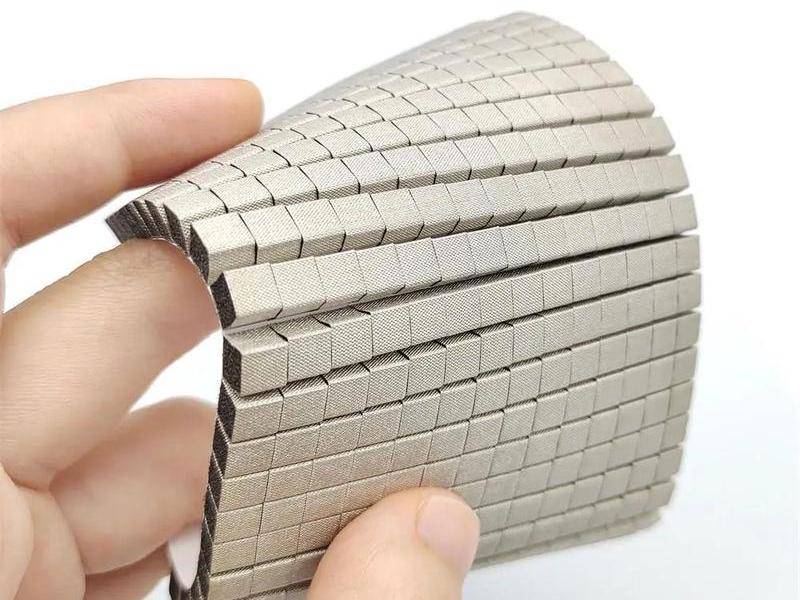
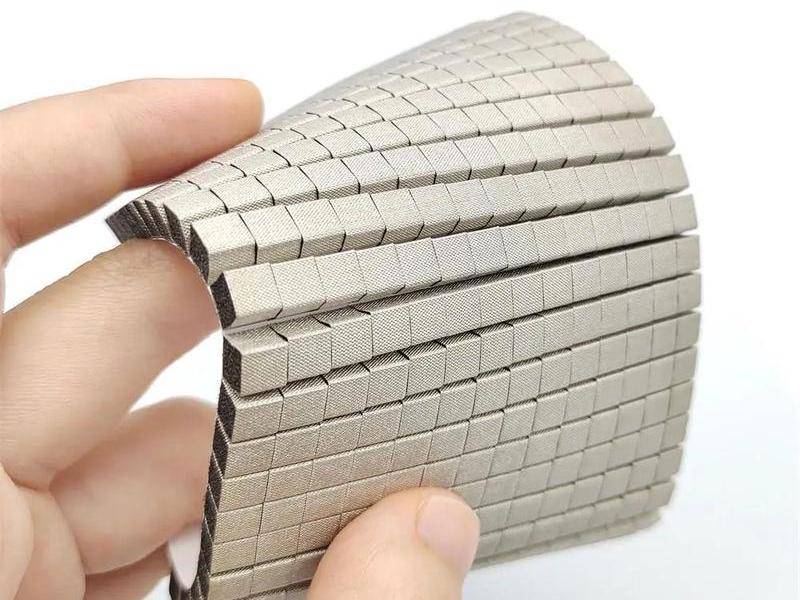
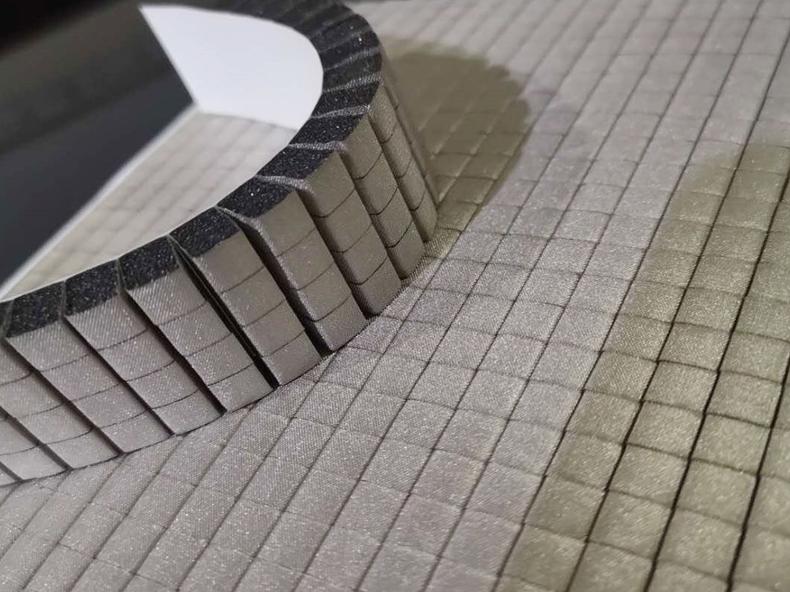
Electrically conductive foam is a specialized foam material that has been infused or coated with conductive materials such as carbon, silver, nickel, or copper. These conductive particles provide the foam with its unique ability to transmit electricity, allowing it to function as both a cushioning material and an electrically active component.
Electrically conductive foam is an innovative material designed to combine the softness, flexibility, and compressibility of traditional foam with the ability to conduct electricity. This unique combination of properties makes conductive foam ideal for a variety of industries where both cushioning and electrical functionality are required, such as electronics, automotive, aerospace, medical devices, and military hardware.
Table of Contents
What is Electrically Conductive Foam?
Electrically conductive foam is a specialized foam material that has been infused or coated with conductive materials such as carbon, silver, nickel, or copper. These conductive particles provide the foam with its unique ability to transmit electricity, allowing it to function as both a cushioning material and an electrically active component.
The foam itself is typically made from polyurethane, polyethylene terephthalate (PET), or other flexible polymers, which provide the base mechanical properties such as compressibility, resilience, and environmental resistance. The conductive fillers are either mixed into the foam during production or applied as a surface coating, depending on the application’s requirements.
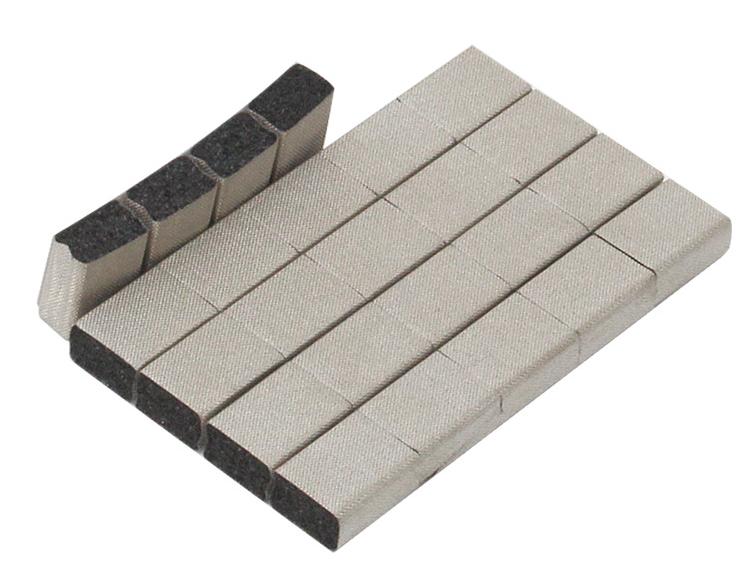
Key Characteristics of Electrically Conductive Foam
Electrically conductive foam offers several distinctive properties that make it suitable for a wide range of applications. Here are the key characteristics that set this material apart:
1. Conductive Fillers
The primary feature of electrically conductive foam is its ability to conduct electricity, which is achieved by adding conductive fillers such as:
- Carbon Black: A cost-effective filler that provides moderate electrical conductivity.
- Silver-Coated Copper Particles: Offers excellent conductivity and is often used in high-performance applications.
- Nickel-Coated Foam: Combines good conductivity with resistance to corrosion, making it ideal for harsh environments.
These conductive fillers are either integrated into the foam’s matrix or applied as a surface layer, ensuring electrical conductivity in all directions.
2. Density and Porosity
Electrically conductive foam is available in various densities and porosities, depending on the application. Low-density foams are typically used for EMI (electromagnetic interference) shielding gaskets, while higher-density foams provide structural support in more demanding environments.
- Low-Density Foam: Lightweight and flexible, suitable for applications requiring minimal compression force.
- High-Density Foam: Offers greater mechanical strength and durability, making it suitable for applications where the foam must provide both electrical conductivity and structural integrity.
3. Environmental Sealing
Electrically conductive foam provides excellent environmental sealing capabilities. It acts as a barrier against dust, moisture, and light water sprays, making it ideal for use in sealing electronic enclosures, outdoor devices, and equipment exposed to harsh environmental conditions.
4. EMI/RFI Shielding
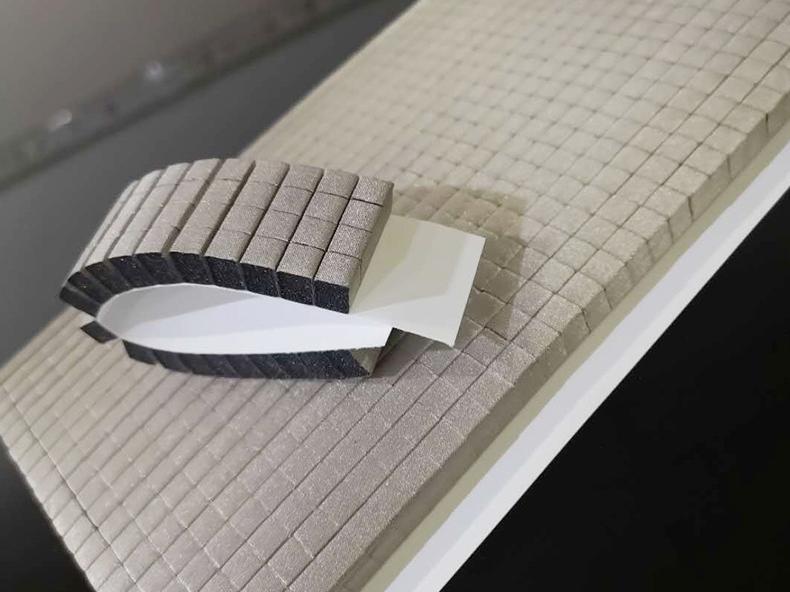
One of the most important applications of electrically conductive foam is its ability to shield electronic devices from EMI and RFI (radio frequency interference). The conductive particles in the foam create a path that blocks or redirects electromagnetic waves, protecting sensitive electronics from external interference.
This property is critical in industries such as telecommunications, aerospace, automotive, and military, where reliable performance of electronic systems is essential.
5. Flexibility and Compression
Electrically conductive foam retains its electrical properties even when compressed. This makes it an ideal material for applications that experience variable pressure points or require repeated compression and relaxation. The foam’s flexibility ensures that it can conform to irregular surfaces while maintaining both its cushioning and conductive functions.
6. Durability and Resistance
Electrically conductive foam is designed to withstand challenging environmental conditions. It is resistant to weathering, temperature extremes, oxidation, and chemicals, ensuring long-term performance in a variety of applications. This durability makes it suitable for outdoor, industrial, and automotive applications where exposure to harsh conditions is common.
Applications of Electrically Conductive Foam
Electrically conductive foam is used across a wide range of industries due to its unique combination of cushioning, sealing, and electrical properties. Below are some of the most common applications:
1. Electronics Enclosures
In electronic devices, conductive foam is used to seal and shield enclosures from external EMI and RFI. It acts as a gasket between the enclosure and the electronic components, preventing interference from external electromagnetic waves and ensuring proper functioning of sensitive devices such as smartphones, computers, and telecommunications equipment.
2. Medical Devices
Electrically conductive foam is used in medical devices where both cushioning and electrical conductivity are required. In applications such as electrostatic discharge (ESD) protection, the foam ensures that static electricity is safely dissipated, preventing damage to sensitive medical equipment.
3. Automotive Industry
In the automotive industry, electrically conductive foam is used in wiring harnesses, sensors, control units, and other components where EMI shielding and vibration dampening are necessary. The foam helps protect sensitive electronics from external interference, ensuring the reliable operation of in-vehicle communication and control systems.
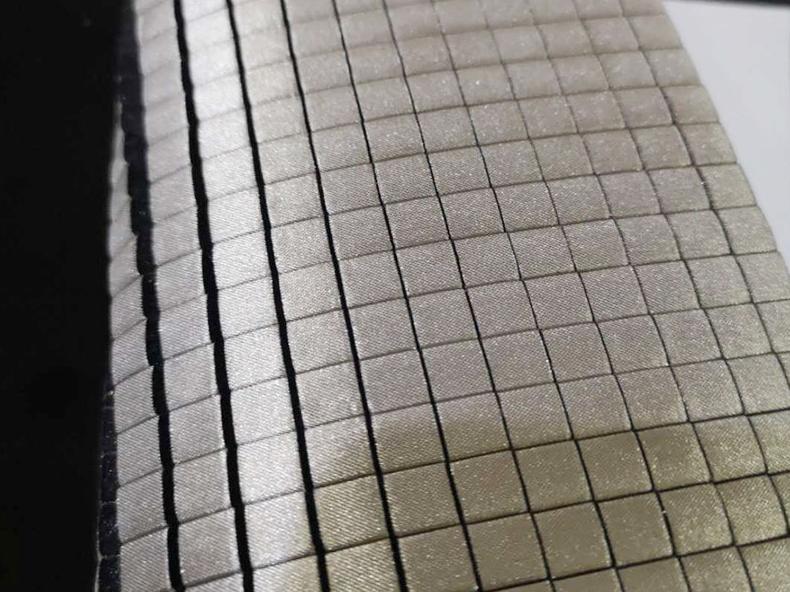
4. Avionics
In avionics systems, electrically conductive foam is used to shield critical electronic components from EMI and RFI. Aircraft electronics are highly sensitive to interference, and conductive foam provides an effective solution for both shielding and sealing enclosures in avionics panels and control systems.
5. Military Hardware
Electrically conductive foam is often used in military applications that require robust EMI shielding and protection against environmental factors. It is used in communication systems, radar equipment, and other high-performance electronics that must operate reliably in harsh environments.
6. Audio Equipment
In audio equipment, conductive foam is used to reduce noise and provide EMI shielding in speakers, microphones, and other audio devices. It helps to minimize interference and ensure clear audio signals in consumer electronics, professional audio equipment, and broadcasting systems.
Manufacturing Process of Electrically Conductive Foam
The production of electrically conductive foam involves several key steps, each designed to ensure that the foam meets the required performance standards for electrical conductivity, mechanical properties, and durability.
1. Foaming Process
The base foam, usually made from materials like polyurethane or PET, is created through a foaming process. During this process, gas bubbles are introduced into the foam, forming a cellular structure that gives the material its characteristic softness and compressibility. The density and porosity of the foam can be controlled during this stage to meet specific application requirements.
2. Conductive Coating or Mixing
Once the foam is produced, conductive particles are either mixed into the foam’s matrix or applied as a surface coating. This can be done through various methods, including:
- Impregnation: The foam is soaked in a conductive solution, which allows the particles to penetrate the material.
- Spraying: Conductive particles are sprayed onto the foam’s surface, creating a thin conductive layer.
- Dipping: The foam is dipped into a bath of conductive material, ensuring even coverage.
The choice of method depends on the desired level of conductivity, thickness, and application requirements.
3. Curing
After the conductive materials are applied, the foam is cured to set its shape and solidify the conductive particles within the foam structure. The curing process ensures that the foam retains its conductivity, flexibility, and mechanical properties over time.
4. Shaping
Once the foam is cured, it can be cut, molded, or shaped into specific sizes and profiles according to the application. This step is critical for ensuring that the foam fits perfectly into the intended application, whether it be a gasket, a sealing strip, or a custom-shaped profile.
5. Testing
Before electrically conductive foam is ready for use, it undergoes rigorous testing to ensure that it meets performance specifications. Tests typically include:
- Conductivity Testing: Ensures that the foam meets the required electrical conductivity standards.
- Compression Set Testing: Verifies that the foam retains its mechanical properties after repeated compression.
- Environmental Testing: Evaluates the foam’s resistance to environmental factors such as temperature, humidity, and chemical exposure.
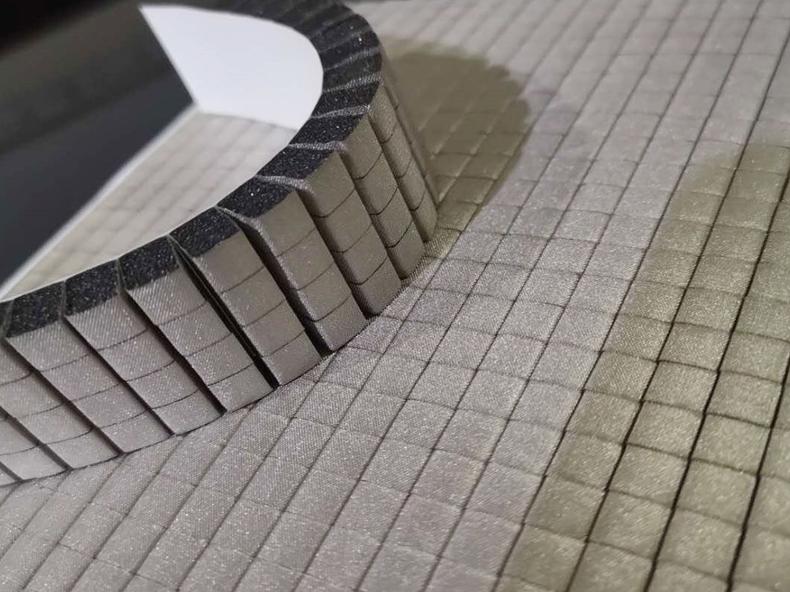
Advancements and Trends in Electrically Conductive Foam
The field of electrically conductive foam is continuously evolving, with new advancements and trends shaping its future. Some of the key developments include:
1. Multi-Functional Materials
Researchers are developing electrically conductive foams that not only conduct electricity but also have additional properties, such as thermal management or flame retardancy. These multi-functional foams provide enhanced performance in applications that require both electrical and thermal conductivity, such as heat sinks or cooling systems for electronic devices.
2. Customization
Manufacturers are increasingly offering tailored formulations of electrically conductive foam to meet specific application needs. For example, conductive foams can be optimized to shield against particular frequencies of EMI/RFI or designed to perform in extreme environmental conditions.
3. Sustainability
As sustainability becomes a priority across industries, there is a growing focus on developing eco-friendly electrically conductive foams. This includes using recyclable materials and reducing waste during production to minimize the environmental impact of manufacturing processes.
Conclusion
Electrically conductive foam is a versatile material that offers a unique combination of electrical conductivity and mechanical flexibility. Its ability to provide EMI shielding, environmental sealing, and electrical continuity makes it an essential component in a wide range of industries, from electronics and automotive to aerospace and military applications.
With advancements in multi-functional materials, customization options, and sustainable manufacturing practices, electrically conductive foam is poised to play an even more significant role in the future of technology. As industries continue to demand materials that offer both physical and electrical properties, electrically conductive foam will remain at the forefront of innovation and performance.If you need them,please contact Handa Shielding righ now.
You May Also Like
-
Handa Canted Coil Springs
Electrical conducting springs
conductive contact finger springs /conducting canted coil springs The Challenge of Maintaining Reliable ConductivityConductive Contact Finger Springs: A Reliable SolutionConsistent Force Across Wide Deflection RangeMultiple Contact Points for Reliable ConductivitySuperior Conductive PropertiesEfficient Heat ManagementEMI/RF Shielding CapabilitiesSupporting SWaP (Space, Weight, and Power) RequirementsLow Insertion Force for Delicate ApplicationsDurability in Challenging ConditionsCleanliness and Sterilization in Medical ApplicationsConclusion: The Versatility of Electrically Conductive Contact Finger Springs Electrically conductive contact finger springs are specialized components designed to serve as highly efficient electrical conductors in applications requiring robust electrical connections, even under challenging conditions such as vibration, dynamic loads, and mechanical shock. These finger springs are often used in various industrial, automotive, and high-tech environments where maintaining electrical integrity is crucial. This article will explore the advantages, applications, and technical considerations of electrically conductive contact finger springs, with an emphasis on their use in environments where consistent electrical conductivity is critical. The Challenge of Maintaining Reliable Conductivity In many industrial settings, maintaining a reliable electrical connection can be a significant challenge. Various operational conditions, such as vibration, mechanical shock, and dynamic loads, can make it difficult for traditional electrical connections to remain secure. For instance, in the petrochemical industry, downhole tools are exposed to extreme......
-
Fingerstrips
Beryllium-copper fingerstrips series
https://www.handashielding.com/contact-us.html Handa Beryllium-Copper Fingerstrips/Fingerstocks with a variety of benefits Introduction to Handa Beryllium-Copper Fingerstrips/FingerstocksOverview of Beryllium-Copper as a MaterialKey Features of Handa Beryllium-Copper Fingerstrips/FingerstocksApplications of Handa Beryllium-Copper Fingerstrips/FingerstocksAdvantages of Using Handa Beryllium-Copper Fingerstrips/FingerstocksInstallation and Best PracticesConclusion Introduction to Handa Beryllium-Copper Fingerstrips/Fingerstocks Handa beryllium-copper fingerstrips, also known as fingerstocks, are highly efficient EMI (Electromagnetic Interference) shielding components. These products are essential in various industries, where sensitive electronic equipment requires protection from external electromagnetic and radio frequency interference (RFI). Beryllium-copper is a popular material for this purpose due to its outstanding combination of mechanical strength, electrical conductivity, and durability. As electronic devices become smaller and more integrated, the demand for highly effective shielding materials has increased. Handa beryllium-copper fingerstrips/fingerstocks provide a versatile solution for shielding gaps, seams, and other openings where electromagnetic radiation can escape or penetrate. This article will explore the design, features, applications, and benefits of these specialized shielding components. Overview of Beryllium-Copper as a Material Before diving into the specifics of Handa's fingerstrips, it is crucial to understand the material used—beryllium copper. Beryllium copper is a copper alloy with small amounts of beryllium (typically 0.5% to 3%). This combination offers several advantages: High Conductivity: Copper is known for its......
-
EMI/EMC Shielding | RFI Shielding | EMI Gaskets
Handa Shielding offers various types of shielding products. These products come in different shapes and materials, and they each have their own unique function. In this article, we will take a look at the EMI shielding aspect and explore the function and advantages of EMI Shielding Helical Springs, which are designed to protect electronic devices from electromagnetic interference. Understanding Electromagnetic Interference (EMI)What Are EMI Shielding Helical Springs?Key Characteristics of EMI Shielding Helical SpringsStructure and Function of EMI Shielding Helical SpringsMaterials Used in EMI Shielding Helical SpringsApplications of EMI Shielding Helical SpringsInstallation and Usage of EMI Shielding Helical SpringsBest Practices for EMI Shielding Helical SpringsConclusion EMI Shielding Helical Springs with Unique Function Understanding Electromagnetic Interference (EMI) Electromagnetic interference (EMI) refers to unwanted noise or interference in an electrical pathway or circuit caused by external sources. Also known as radio frequency interference, EMI can significantly impact the performance and functionality of electronic devices. Key aspects of EMI: It can cause electronics to operate inefficiently, malfunction, or cease functioning entirely EMI can arise from both natural and man-made sources Proper mitigation strategies are essential to minimize its effects What Are EMI Shielding Helical Springs? EMI (Electromagnetic Interference) Shielding Helical Springs are specialized mechanical......
-
EMI/EMC Shielding | RFI Shielding | EMI Gaskets
Handa Endur Shield is a premium electromagnetic interference (EMI) and radio frequency interference (RFI) shielding solution designed to safeguard sensitive electronic equipment from external interference. As the world becomes increasingly reliant on electronics, particularly in critical industries like telecommunications, aerospace, medical technology, and defense, protecting devices from EMI and RFI is crucial. Handa Endur Shield stands out in this domain as a reliable, durable, and customizable product designed for high-performance shielding. What is EMI and Why Does Shielding Matter?Key Features of Handa Endur ShieldMaterials Used in Handa Endur ShieldApplications of Handa Endur Shield Across IndustriesCustomization and Tailored SolutionsConclusion Handa Endur Shield What is EMI and Why Does Shielding Matter? Electromagnetic interference (EMI) refers to the disturbance caused by electromagnetic radiation from one electronic device that affects the functionality of another. This interference can range from mild disruptions to complete system failure, depending on the intensity of the interference and the sensitivity of the affected equipment. RFI (Radio Frequency Interference) is a specific type of EMI that occurs in the radio frequency spectrum. Both EMI and RFI are significant concerns in electronic design, particularly in industries that depend on flawless performance, like aerospace, military, medical, and telecommunications. Shielding is the process......
-
Shielding Gasket Solutions and Materials
Electrically conductive rubber profiles
Electrically conductive rubber profiles represent a unique intersection of material science and engineering, combining the flexibility and sealing properties of traditional rubber with the ability to conduct electricity. This makes them essential in various applications, particularly in sectors where electrical performance and mechanical reliability are critical. These specialized components are manufactured by incorporating conductive fillers, such as carbon black or metal particles, into rubber polymers. This article explores the features, benefits, applications, and manufacturing processes of electrically conductive rubber profiles, shedding light on their importance in modern industrial settings. What Are Electrically Conductive Rubber Profiles?Key Features and BenefitsApplications of Electrically Conductive Rubber ProfilesManufacturing Process of Electrically Conductive Rubber ProfilesConclusion Electrically Conductive Rubber Profiles What Are Electrically Conductive Rubber Profiles? Electrically conductive rubber profiles are rubber components engineered to facilitate the flow of electrical current while retaining the inherent advantages of rubber, such as flexibility, resilience, and sealing capabilities. They are particularly valuable in environments where both electrical and mechanical performance are paramount. Composition and Materials The primary materials used in electrically conductive rubber profiles include: Rubber Polymers: The base material that provides flexibility and durability. Commonly used types include natural rubber, silicone rubber, and neoprene. Conductive Fillers: These materials are......