EMI Shielding Helical Springs with Unique Function
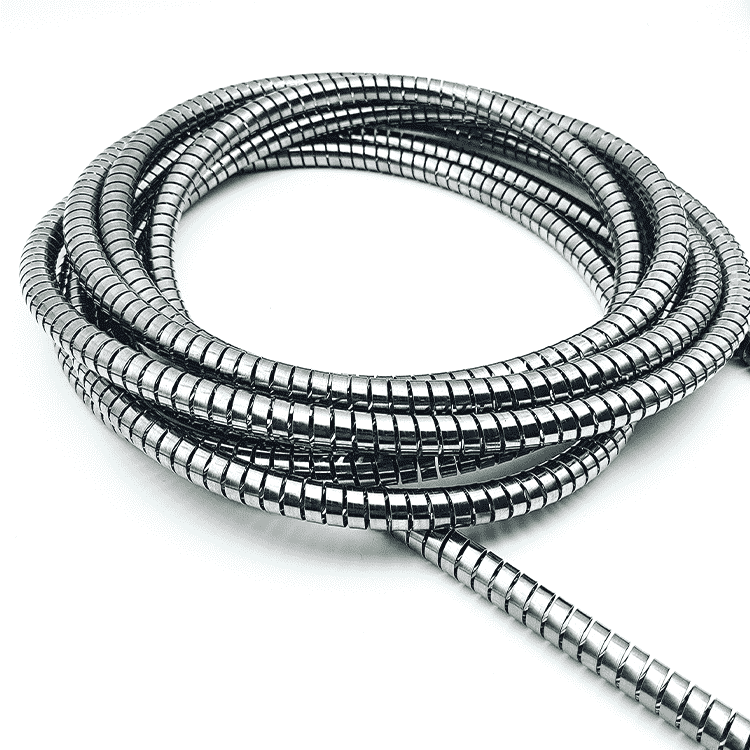
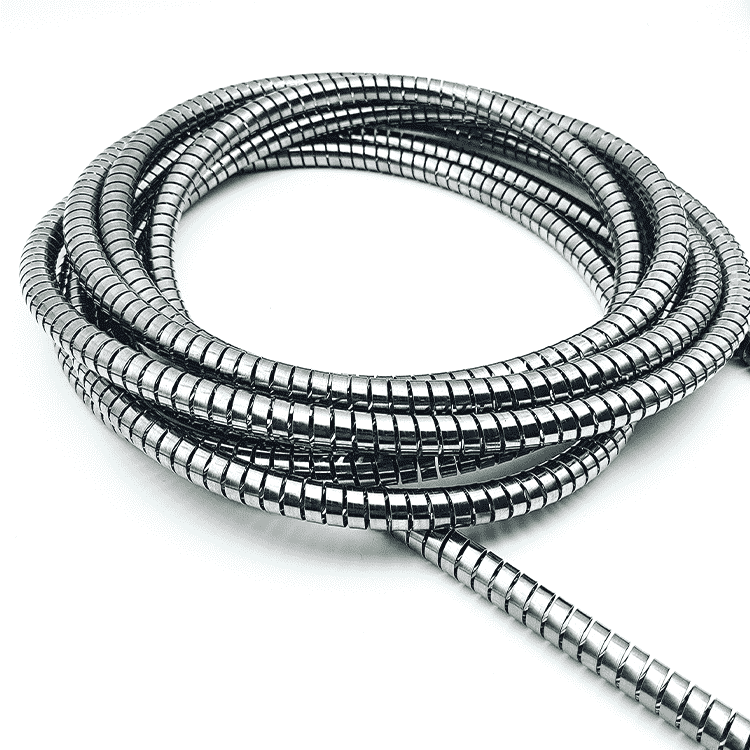
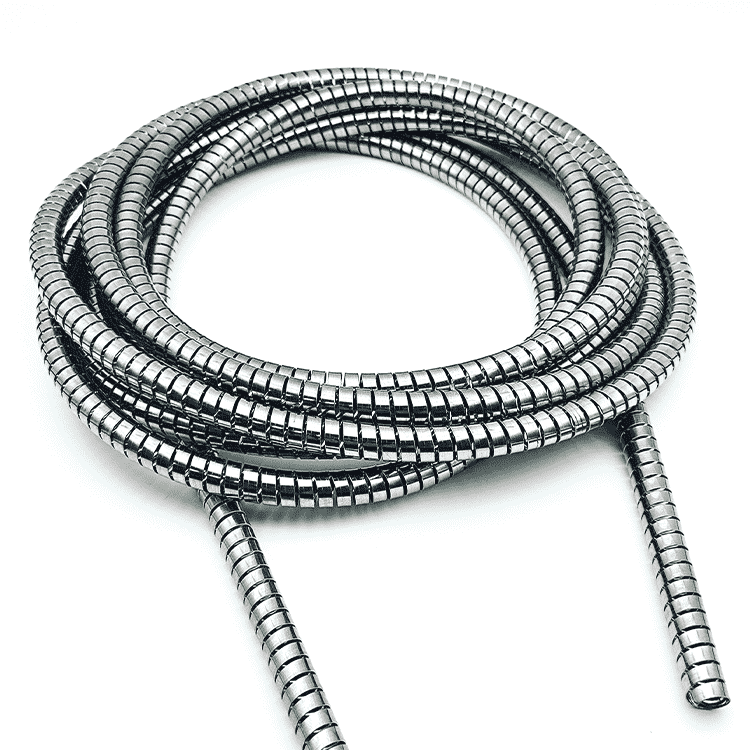
EMI (Electromagnetic Interference) Shielding Helical Springs are specialized mechanical components designed to protect sensitive electronic devices from electromagnetic interference. These springs are characterized by their helical (spiral) shape, typically made from highly conductive materials, which allows them to function both as a mechanical spring and as an EMI shielding solution. Their primary purpose is to provide shielding in applications where electromagnetic radiation can compromise the performance of electronic components.
Handa Shielding offers various types of shielding products. These products come in different shapes and materials, and they each have their own unique function. In this article, we will take a look at the EMI shielding aspect and explore the function and advantages of EMI Shielding Helical Springs, which are designed to protect electronic devices from electromagnetic interference.
Table of Contents
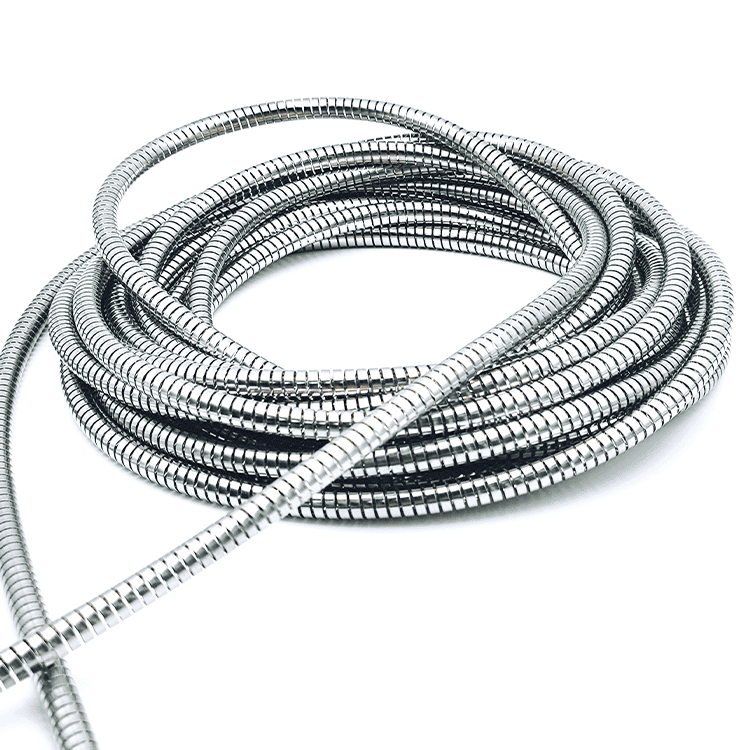
EMI Shielding Helical Springs
with Unique Function
Understanding Electromagnetic Interference (EMI)
Electromagnetic interference (EMI) refers to unwanted noise or interference in an electrical pathway or circuit caused by external sources. Also known as radio frequency interference, EMI can significantly impact the performance and functionality of electronic devices.
Key aspects of EMI:
- It can cause electronics to operate inefficiently, malfunction, or cease functioning entirely
- EMI can arise from both natural and man-made sources
- Proper mitigation strategies are essential to minimize its effects
What Are EMI Shielding Helical Springs?
EMI (Electromagnetic Interference) Shielding Helical Springs are specialized mechanical components designed to protect sensitive electronic devices from electromagnetic interference. These springs are characterized by their helical (spiral) shape, typically made from highly conductive materials, which allows them to function both as a mechanical spring and as an EMI shielding solution. Their primary purpose is to provide shielding in applications where electromagnetic radiation can compromise the performance of electronic components.
These springs act as a protective barrier, preventing unwanted external electromagnetic fields from entering the system and protecting internal components from emitting radiation that could interfere with nearby electronics. The spring’s unique design and structure enable flexibility, durability, and precise shielding, making them particularly effective in applications requiring both mechanical and electromagnetic functionality.
Key Characteristics of EMI Shielding Helical Springs
- Effective EMI Protection:
EMI shielding helical springs offer high attenuation levels, effectively blocking or absorbing electromagnetic waves. This shielding capability ensures that electronic systems remain functional, even in environments where electromagnetic noise is present. - Flexible and Durable:
The helical structure provides flexibility, allowing the spring to adapt to different sizes, shapes, and configurations. This flexibility enables easy installation in various devices, from large enclosures to small, intricate electronic components. - Conductivity:
Made from materials with excellent conductivity, such as copper alloys or stainless steel, these springs provide the dual functionality of shielding and conduction, making them ideal for applications requiring both electrical contact and EMI protection. - Corrosion Resistance:
EMI shielding helical springs are designed to withstand harsh environmental conditions. They often come with protective coatings like silver, nickel, or gold plating, which enhances their corrosion resistance and improves performance in extreme conditions. - Compact Design:
Due to their compact helical design, these springs are ideal for use in small or space-limited electronic enclosures where conventional EMI shielding solutions might be too bulky.
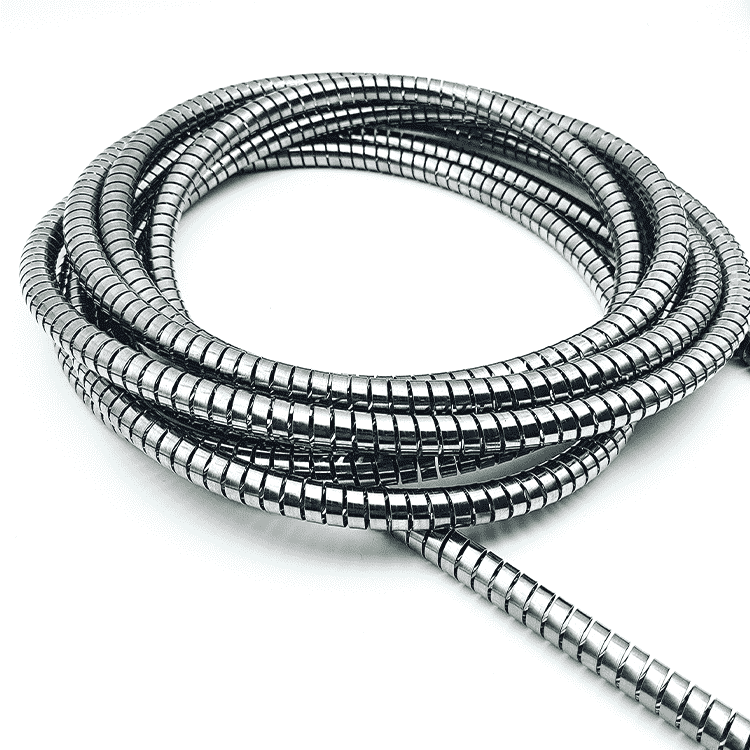
Structure and Function of EMI Shielding Helical Springs
EMI shielding helical springs utilize their unique spiral shape and conductive materials to block or reduce electromagnetic interference. Their effectiveness is primarily based on three key mechanisms:
- Reflection:
The conductive material in the spring reflects the electric component of the EMI. This reflection helps prevent external electromagnetic waves from penetrating the shielded device. - Absorption:
For higher-frequency electromagnetic waves, the spring materials absorb the magnetic component of the EMI. Materials with high magnetic permeability, such as certain stainless steels or nickel alloys, are particularly effective at absorbing EMI. - Multiple Reflections:
The helical design of the spring increases the surface area available for shielding. This shape creates multiple points for reflecting and scattering electromagnetic waves, making it more difficult for the interference to penetrate the shield.
Materials Used in EMI Shielding Helical Springs
The choice of materials for EMI shielding helical springs is critical to ensuring effective performance. Commonly used materials include:
- Beryllium Copper (BeCu):
Beryllium copper is a popular material for EMI shielding springs due to its excellent conductivity, durability, and spring-like properties. It is widely used in industries requiring both electrical contact and EMI protection. - Stainless Steel:
Stainless steel, especially in grades such as 302, 316, and 316L, offers a balance of mechanical strength, corrosion resistance, and shielding effectiveness. Stainless steel is often used in environments where exposure to moisture, chemicals, or high temperatures is a concern. - Silver-Plated or Gold-Plated Springs:
For applications that demand enhanced conductivity, silver or gold plating is applied to the base metal. Silver is particularly valued for its high conductivity and corrosion resistance, making it ideal for applications in harsh environments. - Nickel and Nickel-Plated Copper:
Nickel-plated copper combines the excellent conductivity of copper with the corrosion resistance of nickel, making it a versatile material for EMI shielding in various environments.
The choice of material is often determined by the specific application, environmental conditions, and required level of EMI attenuation.
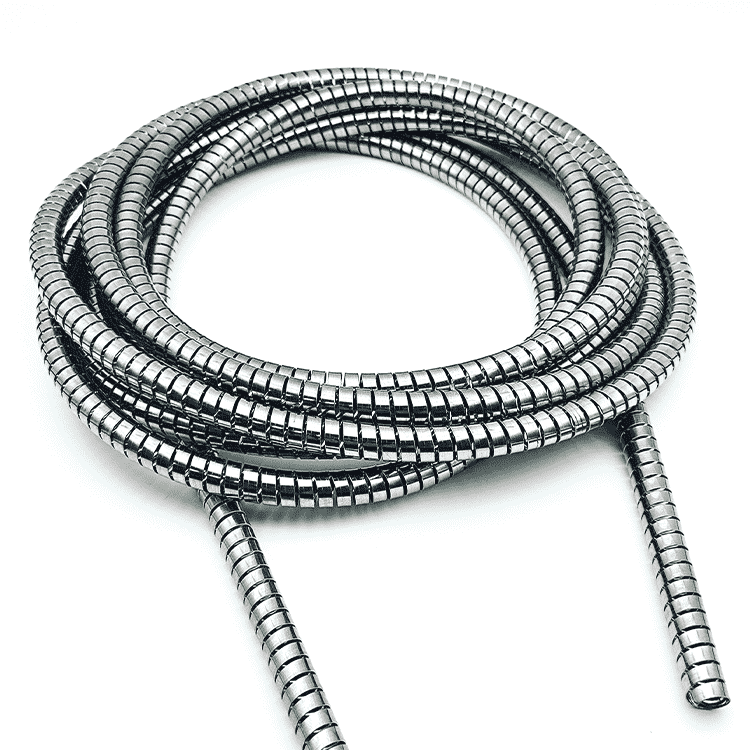
Applications of EMI Shielding Helical Springs
EMI shielding helical springs are used across a wide range of industries where electromagnetic interference is a critical concern. Some of the common applications include:
1. Aerospace and Defense
In aerospace and military applications, where reliability and precision are critical, EMI shielding is essential to protect avionics systems, radar equipment, and communication devices from external electromagnetic radiation. The compact design and durability of helical springs make them suitable for these high-demand environments.
2. Automotive Electronics
Modern vehicles are equipped with advanced electronic systems, such as navigation, infotainment, and advanced driver-assistance systems (ADAS). EMI shielding helical springs help protect these systems from the electromagnetic interference generated by the vehicle’s electrical components and external sources.
3. Medical Devices
In the medical field, devices such as MRI machines, pacemakers, and diagnostic equipment require EMI shielding to ensure accurate results and patient safety. Helical springs provide the necessary protection without compromising the functionality of the devices.
4. Telecommunications Equipment
Telecommunication systems, including satellite communication devices, cell towers, and networking equipment, rely on EMI shielding to maintain signal clarity and prevent disruptions caused by external electromagnetic interference.
5. Consumer Electronics
As the use of wireless devices continues to grow, the need for EMI shielding in consumer electronics has become more pronounced. Smartphones, tablets, and wearable devices require compact EMI shielding solutions, and helical springs offer the flexibility and effectiveness needed for these small, intricate devices.
Installation and Usage of EMI Shielding Helical Springs
Proper installation is essential to ensuring the effectiveness of EMI shielding helical springs. Here is a step-by-step guide for installation:
- Measure the Required Length:
Measure the length of the cable, connector, or component that needs to be shielded to determine the length of the spring required. - Cut to Size:
Using the appropriate cutting tools, cut the spring to the desired length. Ensure that the cut is clean and that the spring’s integrity is maintained. - Install the Spring:
Place the spring over the component or cables that require shielding. Ensure that the spring fits snugly around the component and provides full coverage. - Secure the Spring:
Depending on the application, secure the spring in place using clips, clamps, or adhesive materials to prevent movement during operation.
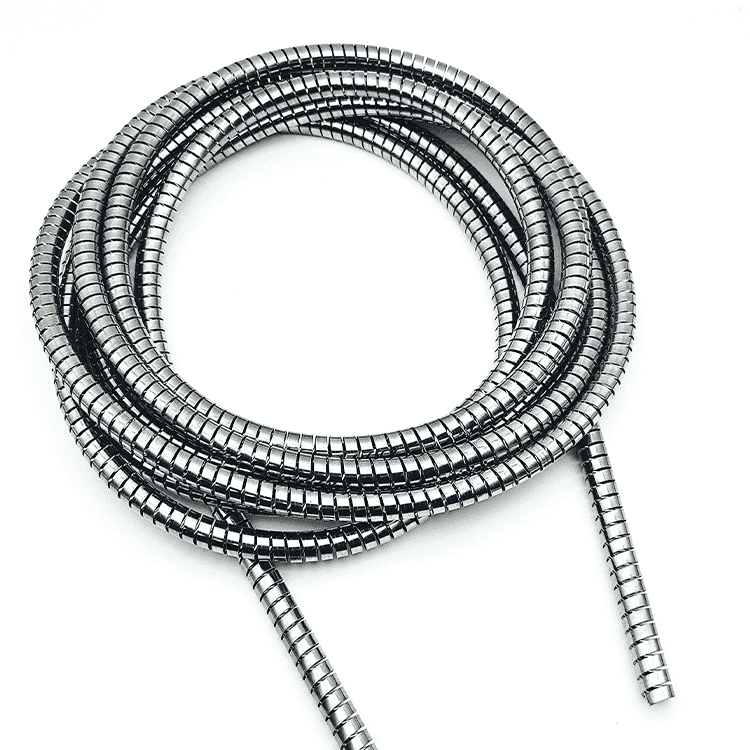
Best Practices for EMI Shielding Helical Springs
To maximize the performance and longevity of EMI shielding helical springs, it is important to follow these best practices:
- Proper Grounding:
Ensure that the shielded components are properly grounded to prevent any leakage of electromagnetic radiation. - Regular Inspection:
Inspect the springs regularly for signs of wear or damage. Replace damaged springs immediately to maintain the integrity of the shielding. - Multiple Layers of Shielding:
For critical applications, consider using multiple layers of shielding. This provides additional protection against high-intensity EMI and ensures redundancy. - Handle with Care:
During installation and handling, avoid damaging the surface of the spring, especially if it has a conductive coating like silver or gold plating.
Conclusion
EMI Shielding Helical Springs play a vital role in protecting electronic systems from electromagnetic interference. Their unique spiral design, combined with the use of highly conductive materials, allows them to provide effective shielding in various industries, including aerospace, automotive, telecommunications, and medical devices. With proper installation, material selection, and adherence to best practices, these springs can significantly improve the performance and reliability of sensitive electronic components.
Their versatility, durability, and effectiveness make them indispensable in today’s increasingly electronic world. As technology continues to evolve, the demand for high-quality EMI shielding solutions like helical springs will continue to grow, ensuring that electronic systems remain safe from the disruptive effects of electromagnetic interference.
You May Also Like
-
EMI/EMC Shielding | RFI Shielding | EMI Gaskets
Handa Endur Shield is a premium electromagnetic interference (EMI) and radio frequency interference (RFI) shielding solution designed to safeguard sensitive electronic equipment from external interference. As the world becomes increasingly reliant on electronics, particularly in critical industries like telecommunications, aerospace, medical technology, and defense, protecting devices from EMI and RFI is crucial. Handa Endur Shield stands out in this domain as a reliable, durable, and customizable product designed for high-performance shielding. What is EMI and Why Does Shielding Matter?Key Features of Handa Endur ShieldMaterials Used in Handa Endur ShieldApplications of Handa Endur Shield Across IndustriesCustomization and Tailored SolutionsConclusion Handa Endur Shield What is EMI and Why Does Shielding Matter? Electromagnetic interference (EMI) refers to the disturbance caused by electromagnetic radiation from one electronic device that affects the functionality of another. This interference can range from mild disruptions to complete system failure, depending on the intensity of the interference and the sensitivity of the affected equipment. RFI (Radio Frequency Interference) is a specific type of EMI that occurs in the radio frequency spectrum. Both EMI and RFI are significant concerns in electronic design, particularly in industries that depend on flawless performance, like aerospace, military, medical, and telecommunications. Shielding is the process......
-
Shielding Gasket Solutions and Materials
Electrically conductive rubber profiles
Electrically conductive rubber profiles represent a unique intersection of material science and engineering, combining the flexibility and sealing properties of traditional rubber with the ability to conduct electricity. This makes them essential in various applications, particularly in sectors where electrical performance and mechanical reliability are critical. These specialized components are manufactured by incorporating conductive fillers, such as carbon black or metal particles, into rubber polymers. This article explores the features, benefits, applications, and manufacturing processes of electrically conductive rubber profiles, shedding light on their importance in modern industrial settings. What Are Electrically Conductive Rubber Profiles?Key Features and BenefitsApplications of Electrically Conductive Rubber ProfilesManufacturing Process of Electrically Conductive Rubber ProfilesConclusion Electrically Conductive Rubber Profiles What Are Electrically Conductive Rubber Profiles? Electrically conductive rubber profiles are rubber components engineered to facilitate the flow of electrical current while retaining the inherent advantages of rubber, such as flexibility, resilience, and sealing capabilities. They are particularly valuable in environments where both electrical and mechanical performance are paramount. Composition and Materials The primary materials used in electrically conductive rubber profiles include: Rubber Polymers: The base material that provides flexibility and durability. Commonly used types include natural rubber, silicone rubber, and neoprene. Conductive Fillers: These materials are......
-
Handa Canted Coil Springs
EMI Shielding Springs
EMI shielding canted coil springs, also known as canted coil springs, are innovative components designed to provide effective electromagnetic interference (EMI) and radio frequency interference (RFI) shielding while also serving as mechanical springs. These springs are characterized by their unique canted coil design, which enables them to provide multiple points of contact for superior EMI shielding, mechanical latching, and electrical conductivity. What Are EMI Shielding Canted Coil Springs?Applications of EMI Shielding Canted Coil SpringsMaterials and Construction of EMI Shielding Canted Coil SpringsBenefits of EMI Shielding Canted Coil SpringsStandards Compliance for EMI Shielding Canted Coil SpringsConsiderations When Using EMI Shielding Canted Coil SpringsConclusion https://www.handashielding.com/contact-us.html What Are EMI Shielding Canted Coil Springs? EMI shielding springs are specialized springs that offer both mechanical and electromagnetic shielding capabilities. Their canted coil design features coils arranged at an angle, which creates multiple points of contact when compressed. This allows the spring to function as both a mechanical component and a highly effective EMI/RFI shield. Electromagnetic interference is a significant concern in modern electronic devices, where external or internal EMI can disrupt signals and affect performance. EMI shielding springs are designed to protect sensitive electronic components from EMI and RFI while also providing mechanical and electrical......
-
EMI/EMC Shielding | RFI Shielding | EMI Gaskets
Fingerstrips
Electromagnetic interference (EMI) can create significant issues for electronic devices and systems, leading to decreased performance, potential malfunction, or even failure. This is where stick-on mounting fingerstrips come in as an essential EMI shielding solution, especially for low-profile, bidirectional applications. These adhesive-backed beryllium-copper strips are designed to be easily installed without the need for specialized tools, providing an efficient and cost-effective way to shield electronics from EMI. In this article, we will explore the features, applications, benefits, and importance of stick-on mounting fingerstrips in EMI shielding. Whether you are working in telecommunications, computer hardware, or any industry where electromagnetic interference poses a risk, stick-on fingerstrips can provide a practical solution. Key Features of Stick-on Mounting Fingerstrips1. Adhesive Backing2. Low-Profile Design3. Beryllium-Copper Construction4. Bi-directional Sealing5. Adjustable SizeApplications of Stick-on Mounting Fingerstrips1. Telecommunications Equipment2. Narrow Electronics Enclosures3. General EMI Shielding Applications4. Computer HardwareBenefits of Stick-on Mounting Fingerstrips1. Easy Installation2. Consistent Sealing3. Flexibility4. Durability5. VersatilityHow Stick-on Mounting Fingerstrips Help with EMI ShieldingMinimizing Electromagnetic InterferenceMaintaining Performance in High-EMI EnvironmentsEnhancing System ReliabilityConclusion Stick-on Mounting Fingerstrips https://www.handashielding.com/contact-us.html Key Features of Stick-on Mounting Fingerstrips When choosing an EMI shielding solution, it’s important to focus on certain key features to ensure that the product you select meets your......
-
EMI/EMC Shielding | RFI Shielding | EMI Gaskets
Fingerstrips
Snap-on mounting fingerstrips are highly effective Electromagnetic Interference (EMI) shielding components used in various electronic enclosures and assemblies to ensure electromagnetic integrity and prevent radio frequency interference (RFI). With the advancement of electronic systems, EMI shielding has become crucial to maintaining the functionality and performance of sensitive electronic devices. Snap-on mounting fingerstrips are designed for easy installation, flexibility, and efficient shielding, making them a popular choice across numerous industries, including telecommunications, military, aerospace, automotive, and consumer electronics. This article will provide a detailed exploration of snap-on mounting fingerstrips, focusing on their key features, materials, installation methods, applications, and benefits. Additionally, we will explore why snap-on mounting fingerstrips are an essential component in modern electronics and how they meet the demands of EMI/RFI shielding requirements. https://www.handashielding.com/contact-us.html What are Snap-On Mounting Fingerstrips?Key Features of Snap-On Mounting FingerstripsTypes of Snap-On Mounting FingerstripsInstallation Method of Snap-On Mounting FingerstripsCommon Applications of Snap-On Mounting FingerstripsMaterial Options for Snap-On Mounting FingerstripsBenefits of Using Snap-On Mounting FingerstripsConclusion: Snap-On Mounting Fingerstrips in EMI Shielding What are Snap-On Mounting Fingerstrips? Snap-on mounting fingerstrips are flexible EMI shielding gaskets made from materials such as beryllium copper, phosphor bronze, or other conductive alloys. They are specifically designed to create a secure electrical......