Electrical Contact Finger Springs
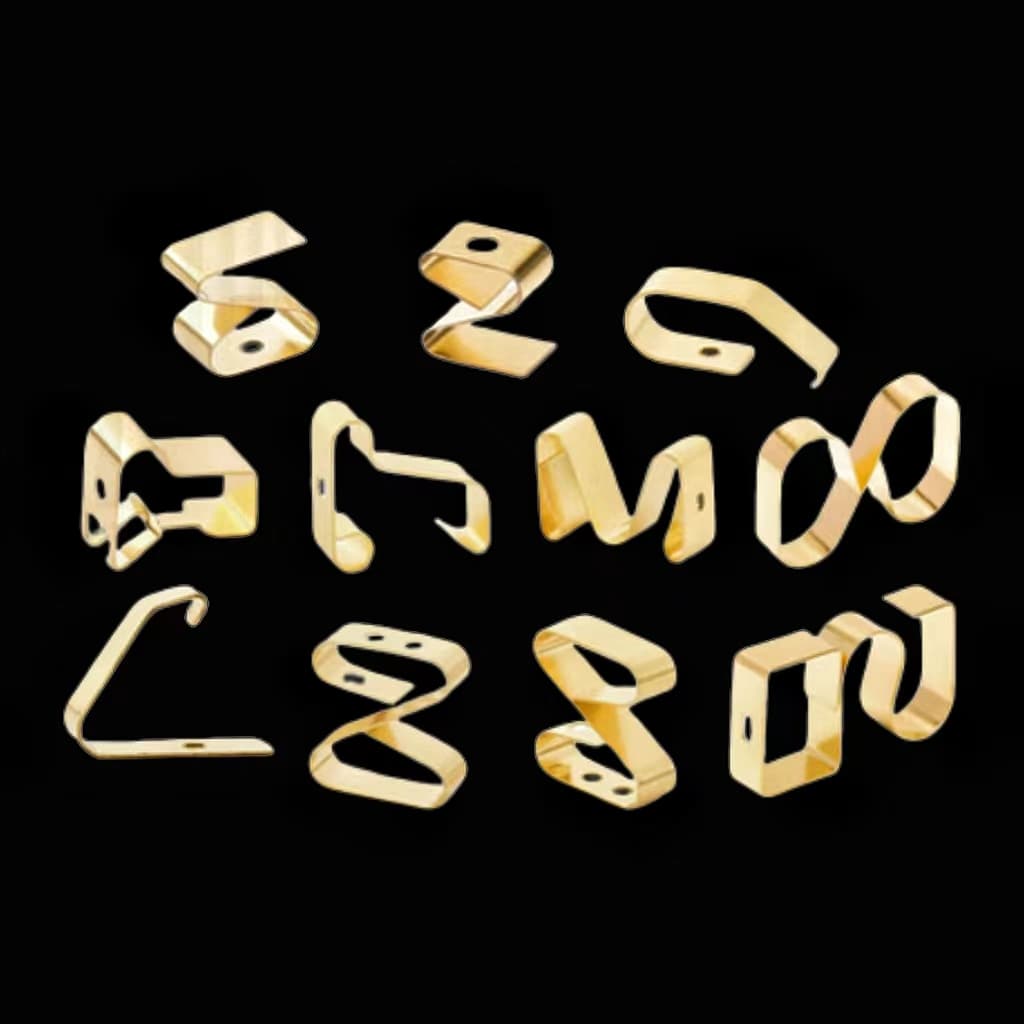
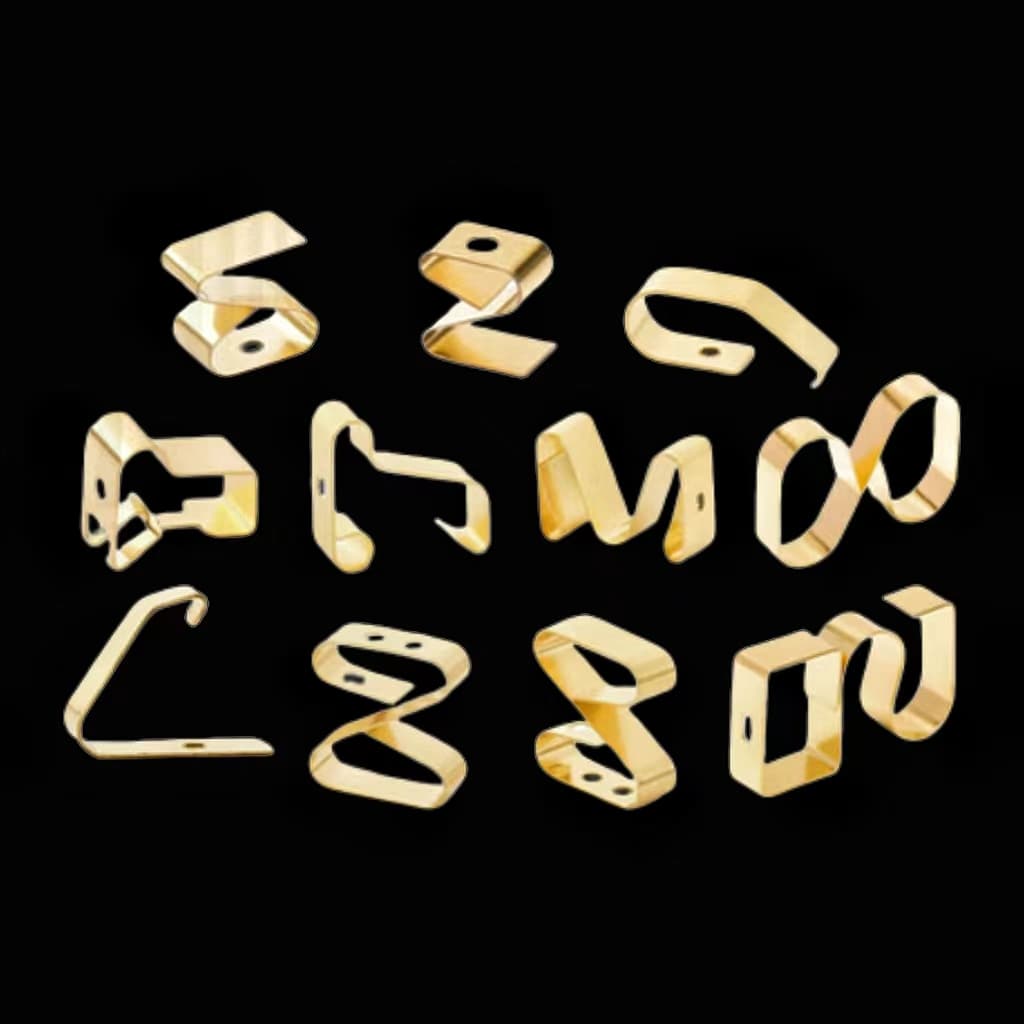
Contact finger springs are crucial components in the field of electronics and electrical engineering. They play a pivotal role in ensuring reliable electrical connections in a wide array of devices and systems.
Introduction to Contact Finger Springs
Contact finger springs are crucial components in the field of electronics and electrical engineering. They play a pivotal role in ensuring reliable electrical connections in a wide array of devices and systems. Understanding these components involves delving into their design, function, materials, and applications. This comprehensive exploration will cover all these aspects in detail.
Table of Contents
Definition and Purpose
Contact finger springs, also known as contact springs or finger contacts, are spring-loaded elements designed to provide a stable and consistent electrical connection between two conductive surfaces. Their primary purpose is to maintain a secure and reliable electrical connection by applying a constant force between the contacts, which helps to minimize issues like intermittent connections, wear, and poor conductivity.
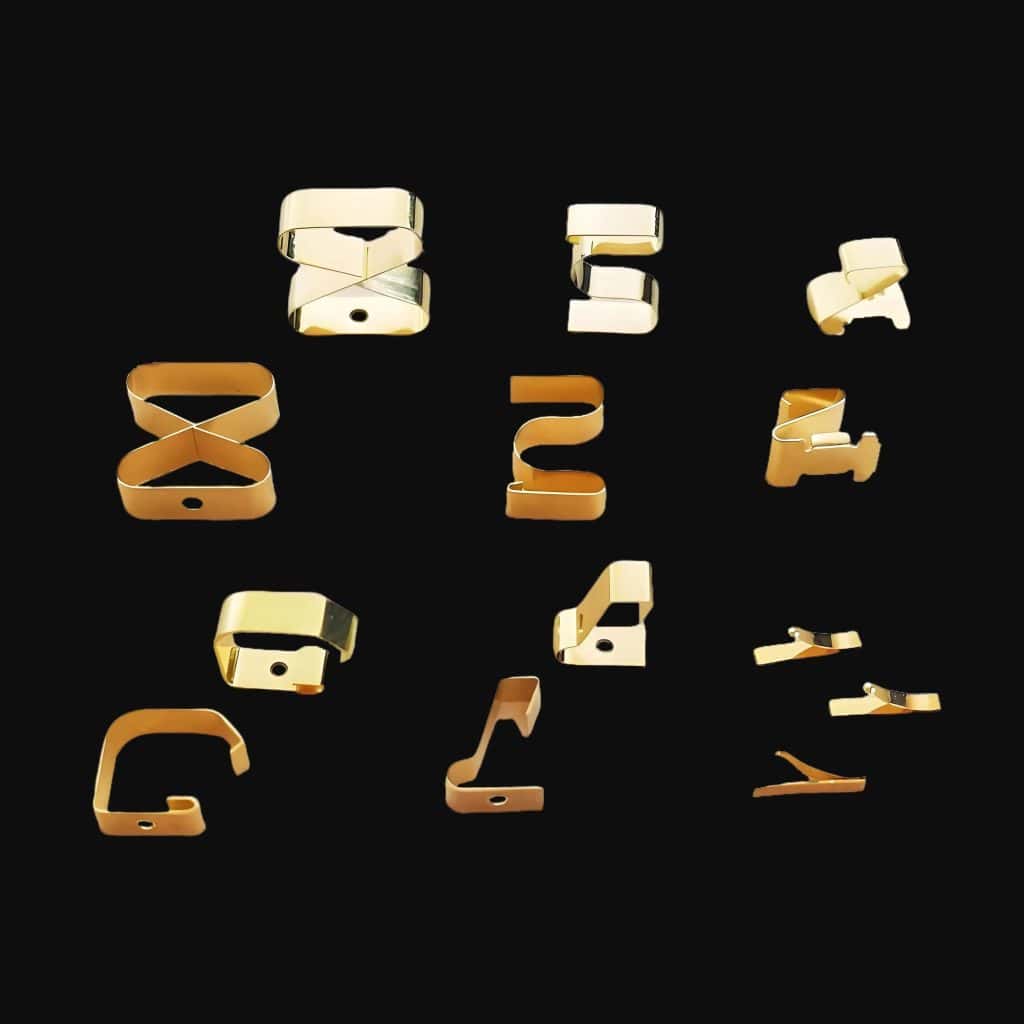
Design and Functionality
1. Design Elements
- Shape and Structure: Contact finger springs are typically designed with a specific geometric shape that allows them to compress and return to their original form. Common designs include flat, curved, or cylindrical shapes. The design often resembles a comb or series of fingers, which is why they are sometimes referred to as “finger” springs.
- Material Composition: The conductive materials used in contact finger springs are chosen for their electrical conductivity and mechanical flexibility.
- Spring Mechanism: The spring mechanism is designed to provide a specific amount of pressure to ensure good contact. This pressure is crucial for overcoming any irregularities on the surfaces being connected and for maintaining contact over time.
2. Functionality
- Electrical Contact: The primary function of a contact finger spring is to maintain a reliable electrical connection. When two conductive surfaces are connected, the finger spring exerts a force that ensures consistent contact, reducing the risk of electrical interruptions.
- Compensation for Tolerance: In manufacturing, components may not always fit perfectly due to tolerances. Contact finger springs can compensate for these tolerances by adjusting their position slightly to maintain a good connection.
- Wear Resistance: Over time, repeated connections and disconnections can cause wear on the contact surfaces. Contact finger springs help to mitigate this by ensuring that pressure is consistently applied, which helps in reducing the wear and tear on both the spring and the contact surfaces.
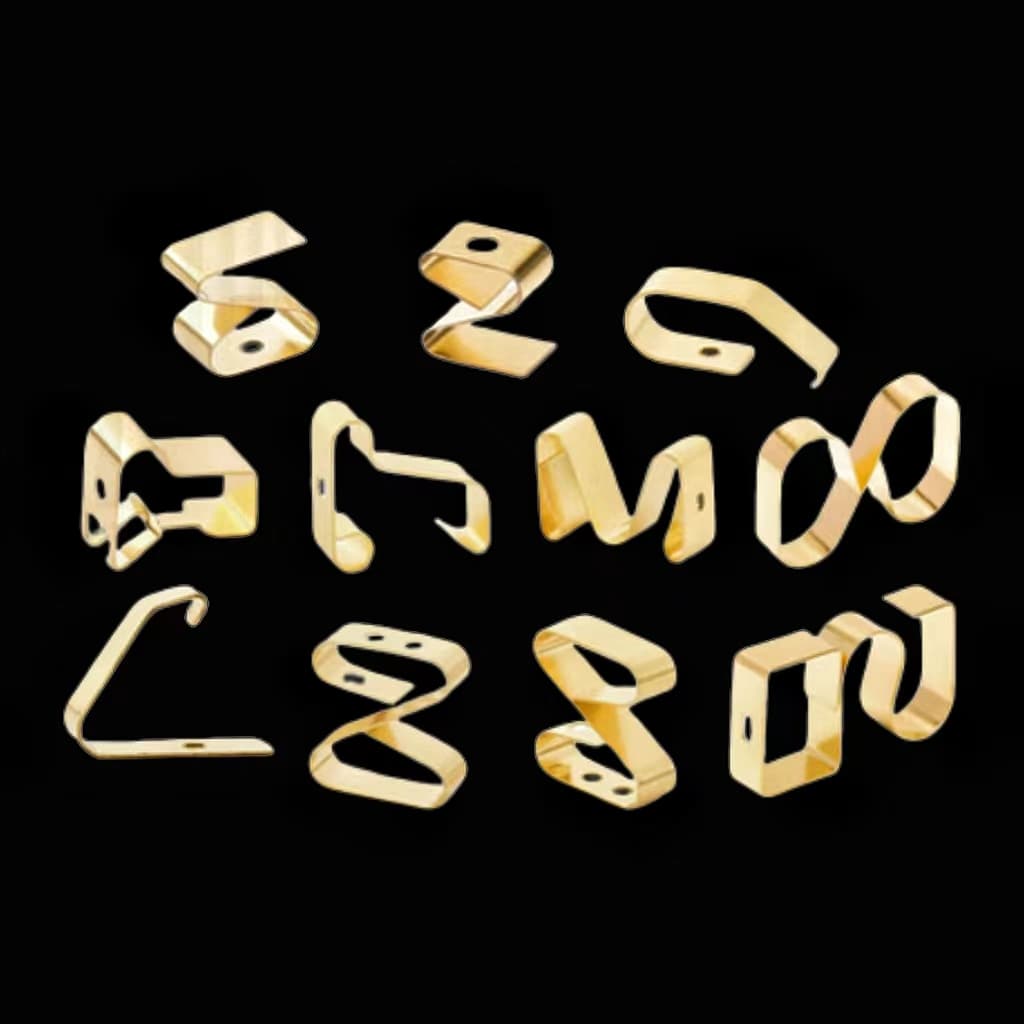
Materials and Manufacturing
1. Material Selection
- Stainless Steel: Offers high resistance to corrosion and is used in environments where exposure to moisture or chemicals is a concern. Stainless steel springs are durable and can withstand harsh conditions.
- Copper Alloys: Include materials such as brass and beryllium copper. These alloys are favored for their superior electrical conductivity, which is essential for applications where minimizing electrical resistance is critical.
- Phosphor Bronze: Known for its excellent mechanical properties and resistance to fatigue. It also has good electrical conductivity, making it suitable for many contact spring applications.
2. Manufacturing Processes
- Stamping: A common process used to create contact finger springs, where sheets of metal are cut and shaped using a stamping press. This method is efficient for producing large quantities of springs with consistent dimensions.
- Precision Cutting: Involves cutting the springs to exact specifications using laser or water jet cutting techniques. This method is used for applications requiring very precise dimensions and shapes.
- Heat Treatment: To enhance the mechanical properties of the springs, they may undergo heat treatment processes such as annealing or tempering. This treatment improves the spring’s strength and flexibility.
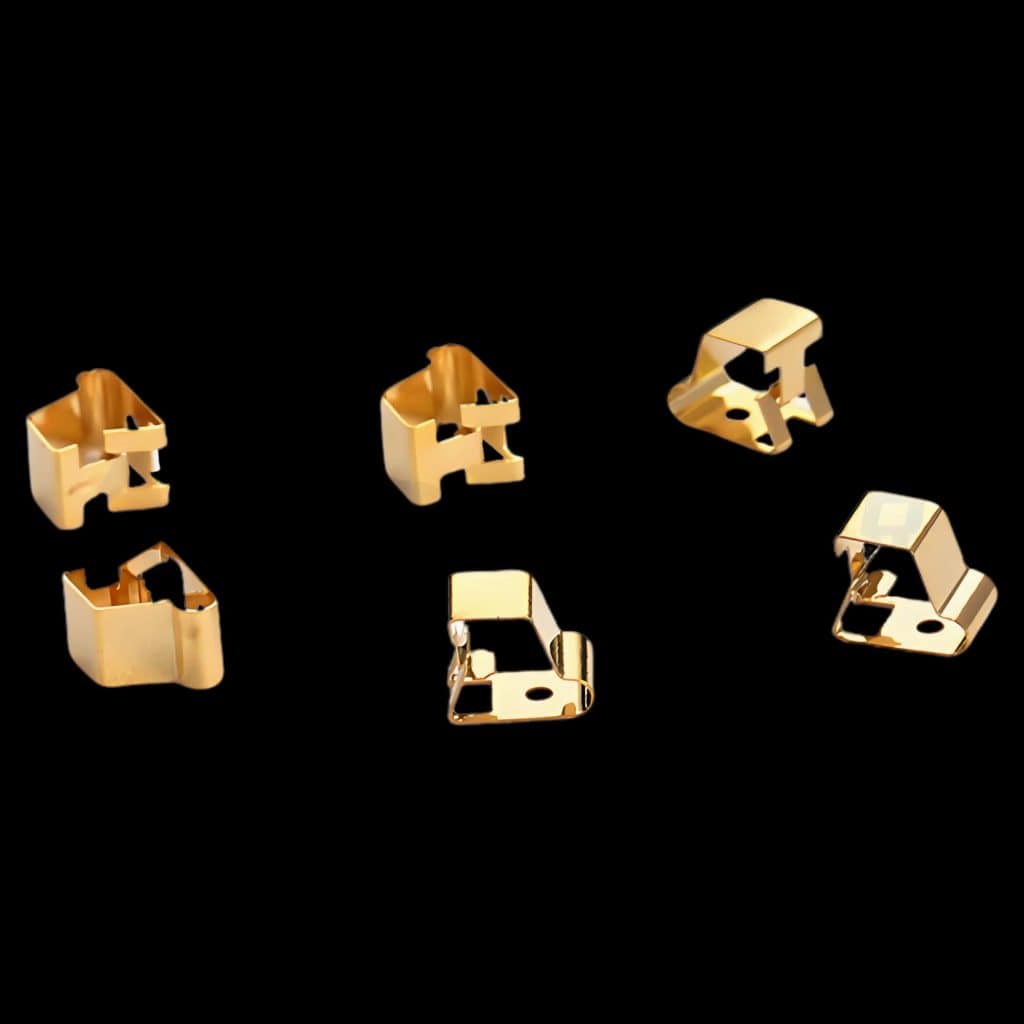
Applications
Contact finger springs are used in various applications across different industries. Here are some notable examples:
1. Electronic Connectors
In electronic connectors, contact finger springs are employed to ensure a reliable connection between the connector and the mating component. This is particularly important in high-density connectors where space is limited, and the reliability of the connection is paramount.
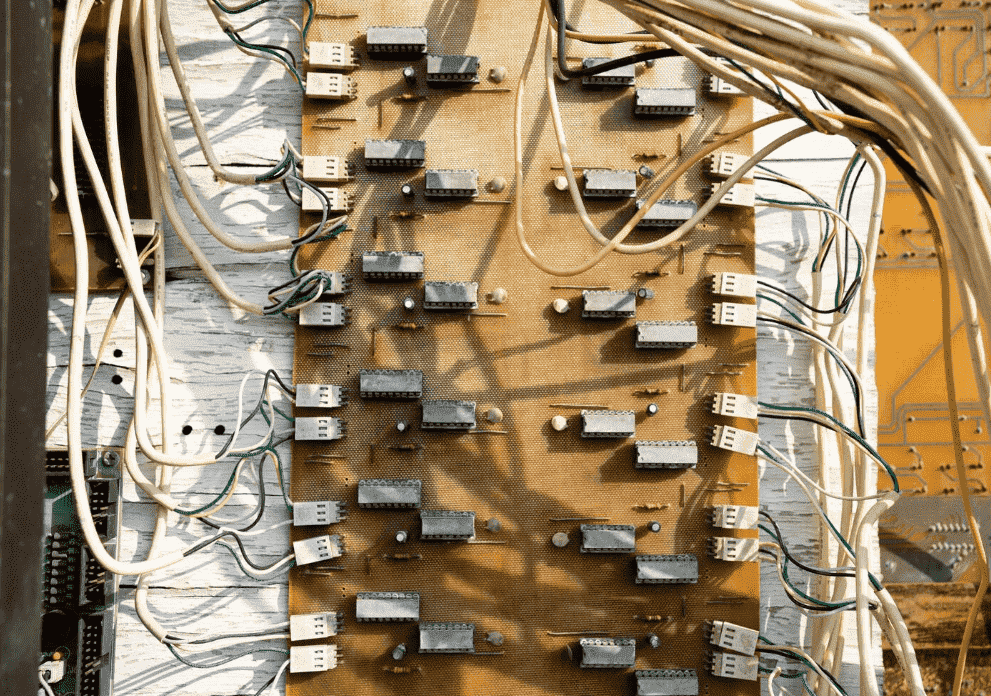
2. Switches
Contact finger springs are used in mechanical switches to maintain consistent contact between the switch’s moving parts. This ensures that the switch functions properly and provides a reliable electrical connection when activated.
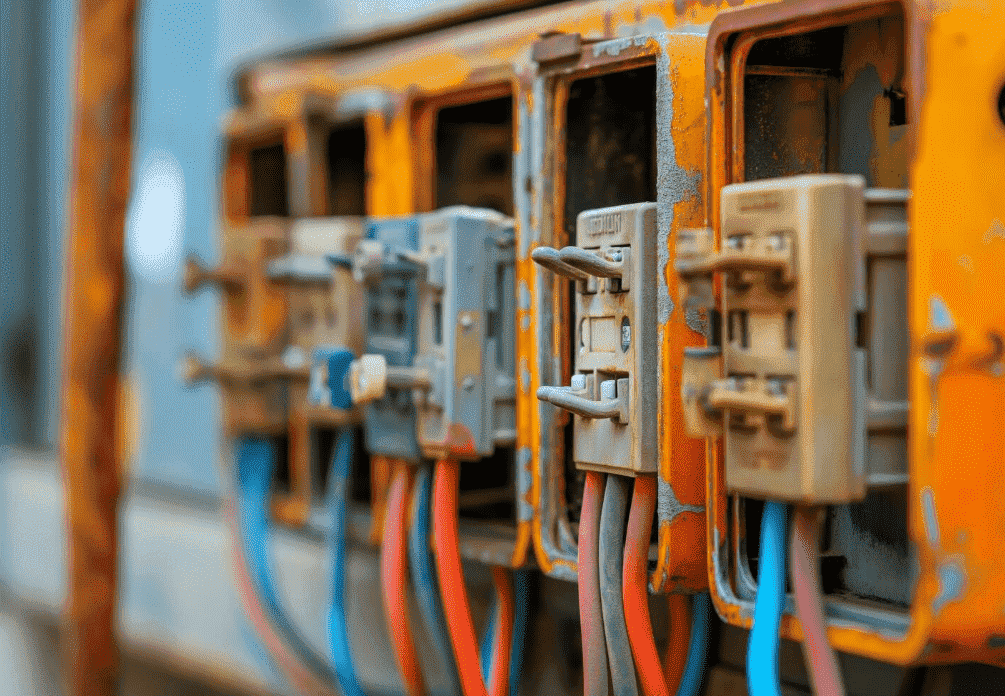
3. Circuit Boards
In circuit boards, contact finger springs are used to connect different layers of the board or to provide connections between the board and external components. They help in maintaining a stable electrical connection despite any thermal expansion or mechanical stresses.
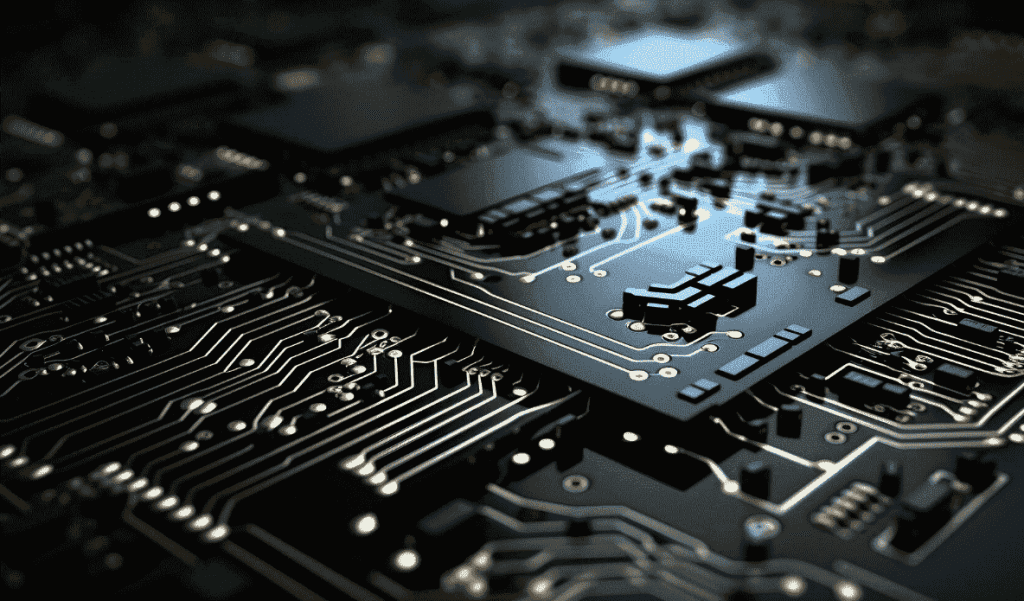
4. Automotive Applications
In automotive electronics, contact finger springs are used in various components such as connectors, switches, and sensors. Their durability and reliability are crucial for the proper functioning of automotive electrical systems, which are exposed to vibrations, temperature changes, and other harsh conditions.
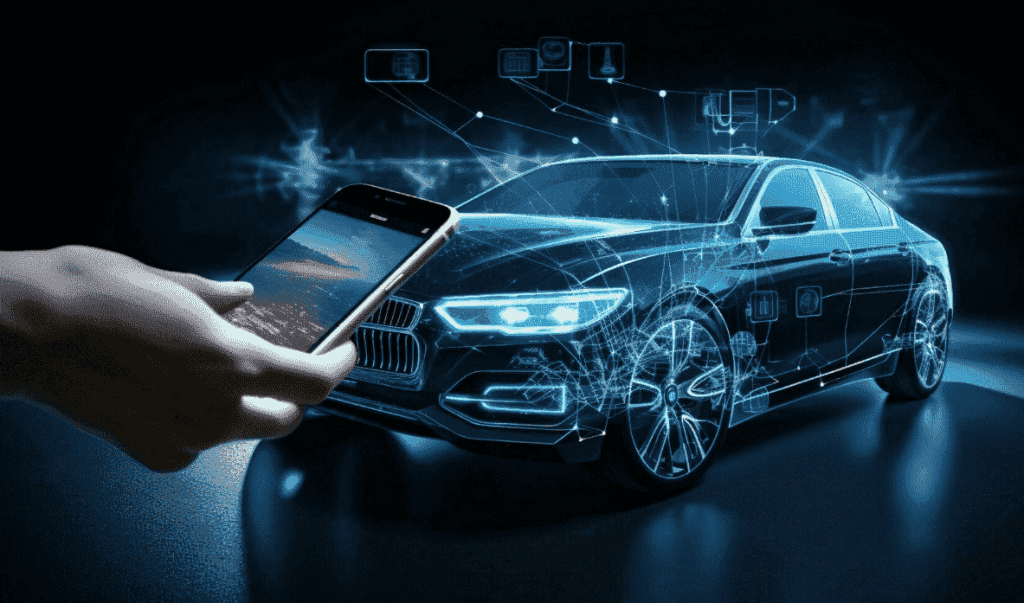
5. Consumer Electronics
Contact finger springs are also found in consumer electronics, such as mobile phones, laptops, and other portable devices. They ensure reliable connections between different components within these devices, contributing to their overall performance and longevity.
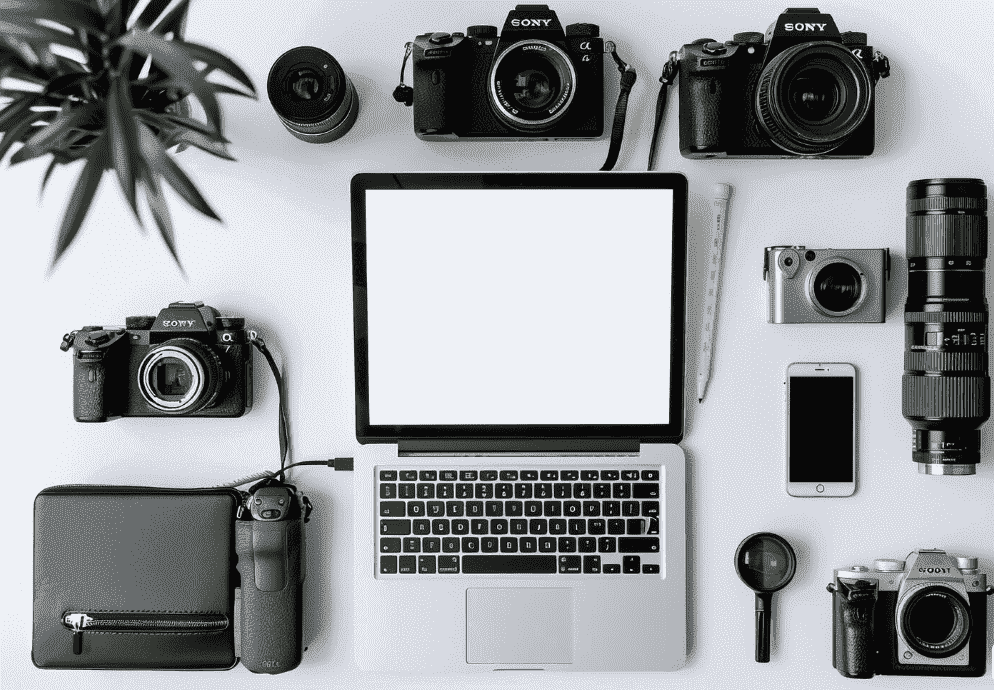
Benefits and Limitations
1. Benefits
- Reliability: Contact finger springs provide a reliable connection by applying consistent pressure, which helps in reducing the risk of intermittent connections and signal loss.
- Durability: Made from high-quality materials, contact finger springs are designed to withstand repeated use and exposure to various environmental conditions.
- Compensation for Tolerances: They help in compensating for manufacturing tolerances and surface irregularities, ensuring a good connection even in less-than-perfect conditions.
2. Limitations
- Wear and Tear: Over time, contact finger springs may experience wear and tear, which can affect their performance. Regular maintenance and replacement may be required in some applications.
- Cost: High-quality contact finger springs made from specialized materials can be expensive. However, their benefits in terms of reliability and performance often outweigh the cost.
- Design Complexity: The design of contact finger springs can be complex, especially in applications requiring precise dimensions and performance characteristics. This complexity can lead to higher manufacturing costs and design challenges.
Future Trends and Developments
As technology continues to evolve, there are several trends and developments in the field of contact finger springs:
1. Miniaturization
With the trend towards smaller and more compact electronic devices, there is an increasing demand for miniaturized contact finger springs. Advances in materials and manufacturing techniques are enabling the production of smaller, more precise springs without compromising performance.
2. Advanced Materials
New materials and alloys are being developed to enhance the performance of contact finger springs. These materials offer improved conductivity, durability, and resistance to environmental factors, contributing to the overall reliability of electronic components.
3. Enhanced Manufacturing Techniques
Advancements in manufacturing technologies, such as 3D printing and precision machining, are enabling the production of more complex and customized contact finger springs. These techniques allow for greater design flexibility and the ability to meet specific application requirements.
Conclusion
Contact finger springs are essential components in modern electronics and electrical systems, providing reliable and consistent electrical connections. Their design, materials, and applications are diverse, reflecting their importance in ensuring the proper functioning of various devices and systems. Understanding their functionality, benefits, and limitations can help in selecting the right components for specific applications and in addressing any challenges related to their use. As technology continues to advance, contact finger springs will continue to evolve, contributing to the ongoing development of electronic and electrical systems.
You May Also Like
-
Shielding Gasket Solutions and Materials
EMI shielding gaskets
Knitted metal wire mesh gaskets are engineered using fine metal wires, typically stainless steel or other conductive alloys, that are knitted or woven into a mesh structure. This design enables the gaskets to conform closely to mating surfaces, providing a continuous and reliable conductive path for shielding against EMI. The flexibility and resilience of knitted metal wire mesh gaskets make them suitable for sealing gaps and joints in electronic enclosures, effectively blocking electromagnetic radiation across a wide frequency range. Key Features and BenefitsApplications Across Industries Key Features and Benefits High Shielding Effectiveness: Knitted metal wire mesh gaskets offer high shielding effectiveness due to their dense, conductive mesh structure. They attenuate electromagnetic waves and prevent external interference from disrupting sensitive electronic signals, ensuring optimal device performance. Versatility: Available in various shapes, sizes, and configurations, these gaskets can be customized to fit specific application requirements. They are used in diverse industries such as telecommunications, aerospace, automotive, medical devices, and industrial automation. Durability and Longevity: Constructed from durable materials such as stainless steel, knitted metal wire mesh gaskets exhibit excellent mechanical strength and corrosion resistance. They withstand environmental factors and maintain shielding integrity over extended periods, reducing maintenance costs and downtime. Conductive Resilience:......