Handa spiral tubes with remarkable performance in EMI shielding applications
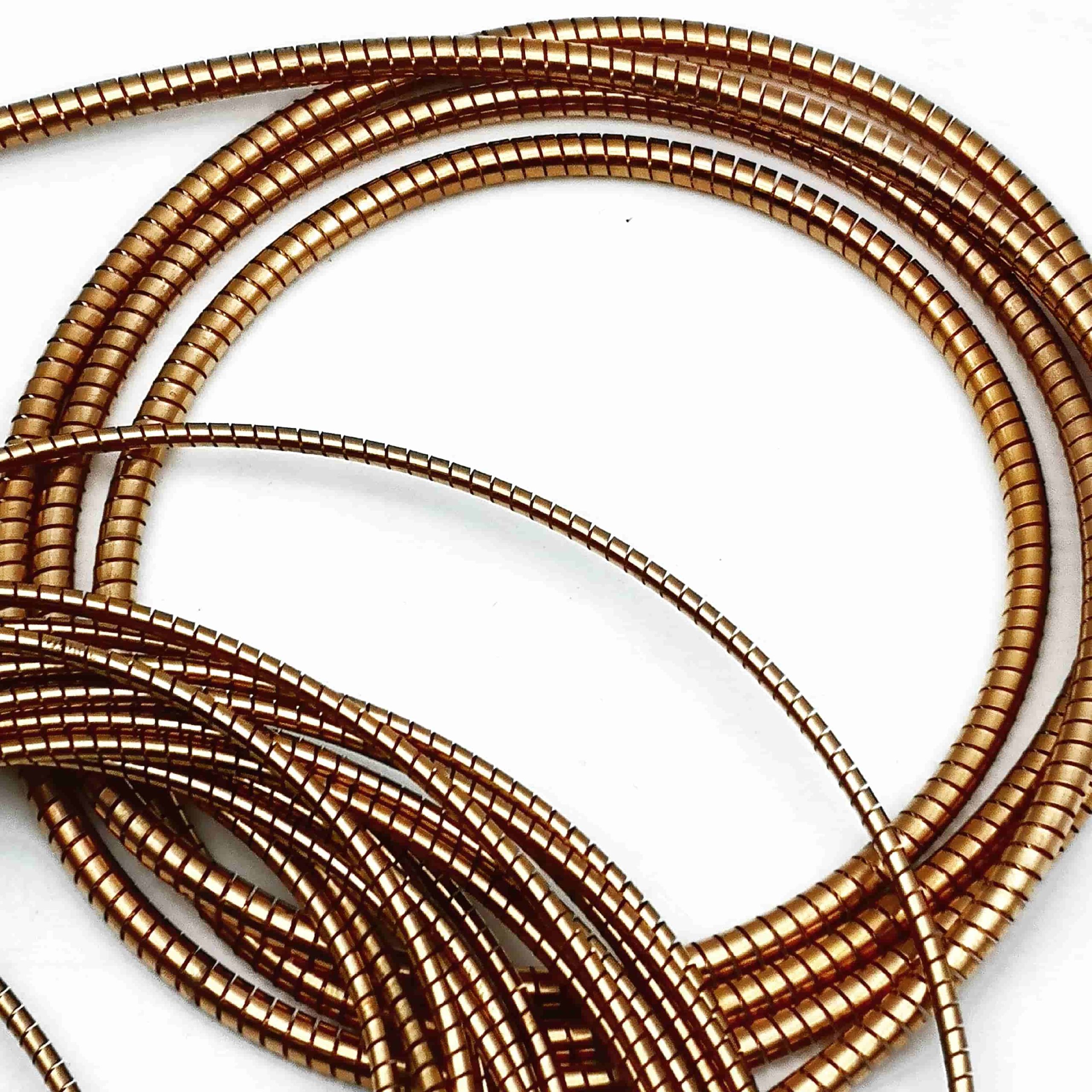
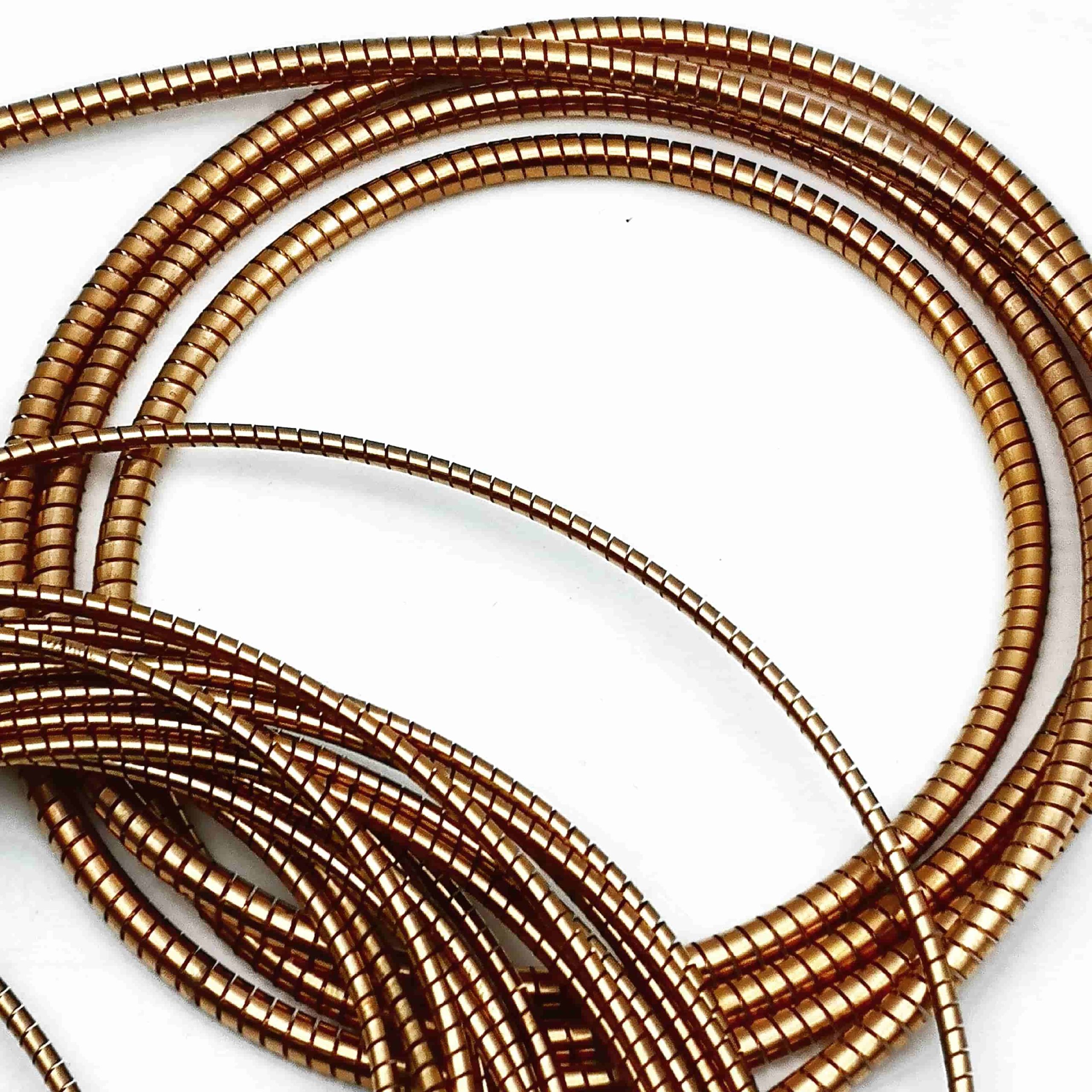
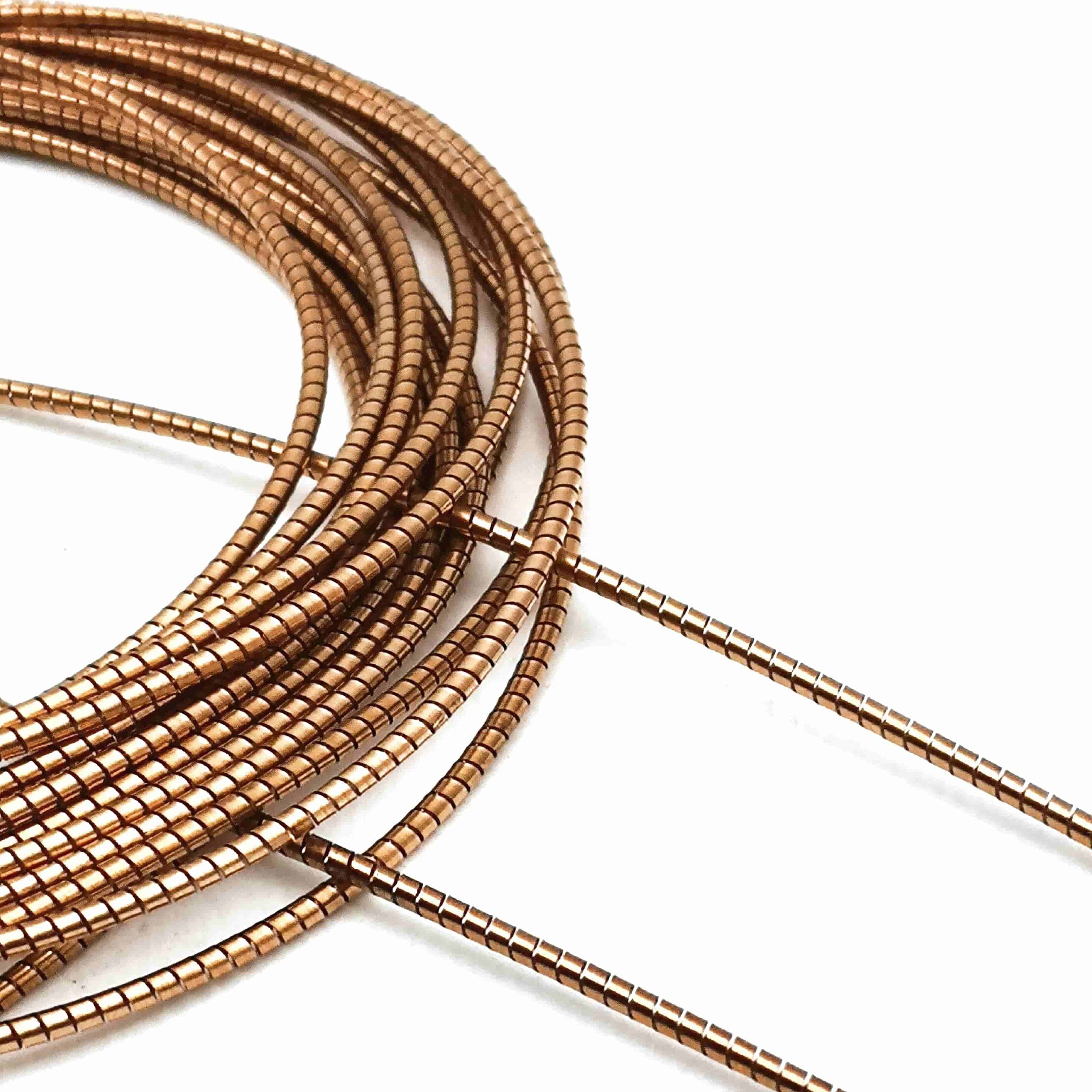
Handa spiral tubes are known for their remarkable performance in EMI shielding applications, particularly in humid or otherwise challenging environments. This functionality is largely due to the unique characteristics of their material composition and surface treatments. These tubes have become invaluable across industries, including telecommunications, aerospace, military, medical, and precision instrumentation, where reliable EMI shielding is crucial.
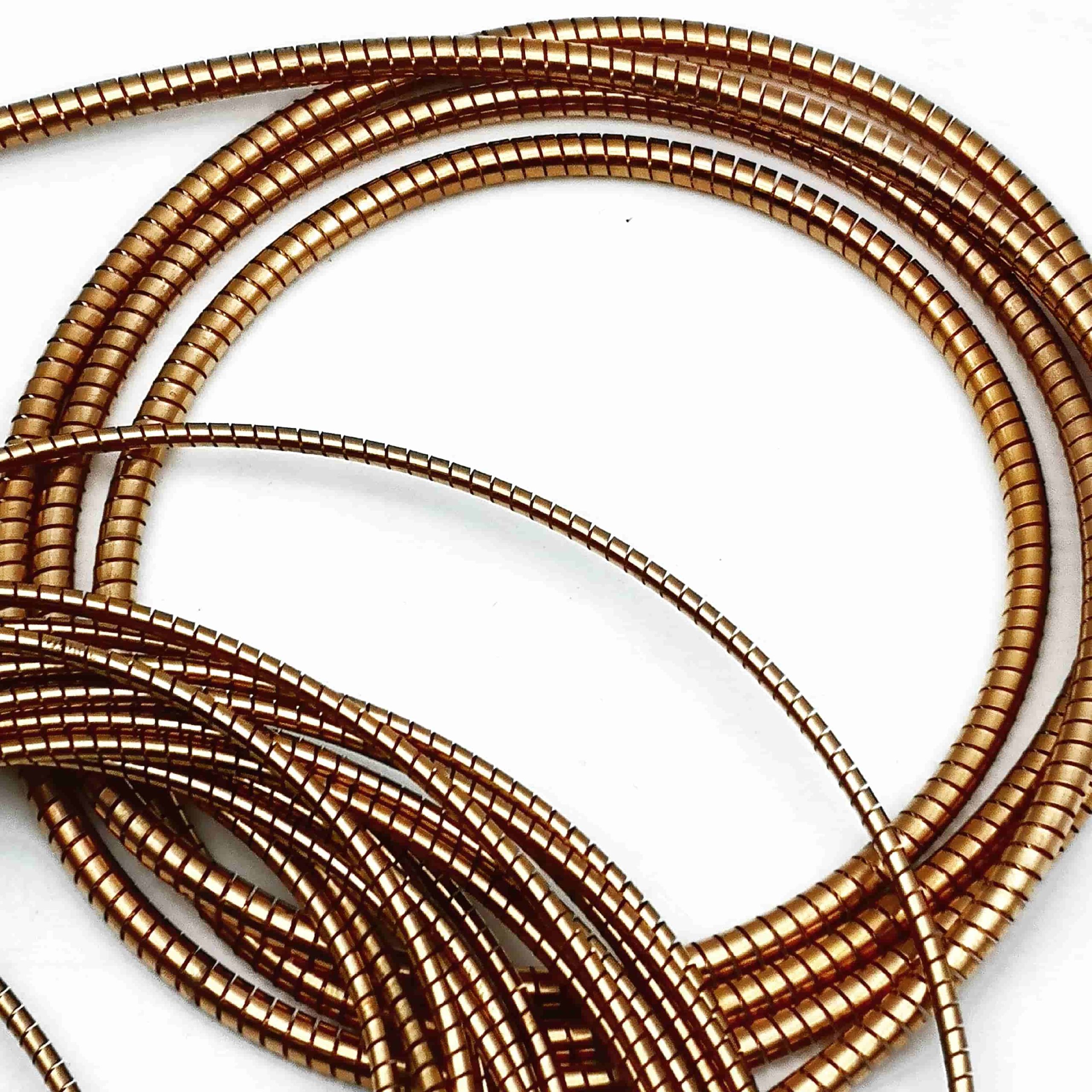
Handa spiral tubes
Table of Contents
Handa spiral tubes are known for their remarkable performance in EMI shielding applications, particularly in humid or otherwise challenging environments. This functionality is largely due to the unique characteristics of their material composition and surface treatments. These tubes have become invaluable across industries, including telecommunications, aerospace, military, medical, and precision instrumentation, where reliable EMI shielding is crucial. Here is an expanded look at the comprehensive advantages, applications, and technological features of Handa spiral tubes, focusing on their functionality in humid conditions and their material properties.
Material Properties of Handa Spiral Tubes
The effectiveness of Handa spiral tubes in EMI shielding applications is largely a result of the materials used in their construction. The primary materials are:
- Beryllium Copper (BeCu):
- High Conductivity: Beryllium copper is widely recognized for its high electrical conductivity, which enables efficient electromagnetic wave transmission. This quality makes BeCu an excellent material for EMI shielding, allowing it to absorb and reflect interfering signals.
- Elasticity and Mechanical Resilience: Beryllium copper has exceptional elasticity, which allows the tubes to compress and return to their original shape repeatedly without sustaining damage. This feature is critical for long-term reliability in applications where the tube may be subjected to fluctuating pressures or vibrations.
- Fatigue Resistance: The fatigue resistance of BeCu is among its standout properties, making it ideal for applications requiring repeated flexing or compression without material degradation. This is particularly useful for applications in environments with varying temperature and humidity, where material stability is essential.
- Stainless Steel 316 (SS316):
- Corrosion Resistance: Stainless steel 316 is known for its superior resistance to corrosion, especially in moist or saline conditions. This quality makes it well-suited for applications in marine environments or areas with high humidity.
- Improved Conductivity Through Tin Plating: Stainless steel 316, when tin-plated, has an even higher level of electrical conductivity. This improvement is essential for EMI shielding as it ensures more efficient signal blockage and absorption.
- Surface Coating and Treatment:
- Tin Plating: Tin plating enhances the tube’s conductivity, which is critical for maintaining effective EMI shielding. Additionally, the tin layer adds another barrier against corrosion, especially in environments with high humidity.
- Edge Coating: Edge coatings provide protection against electrochemical corrosion, which is common in damp or saline environments. This treatment further enhances the durability and shielding effectiveness of Handa spiral tubes, even when exposed to moisture and salt.
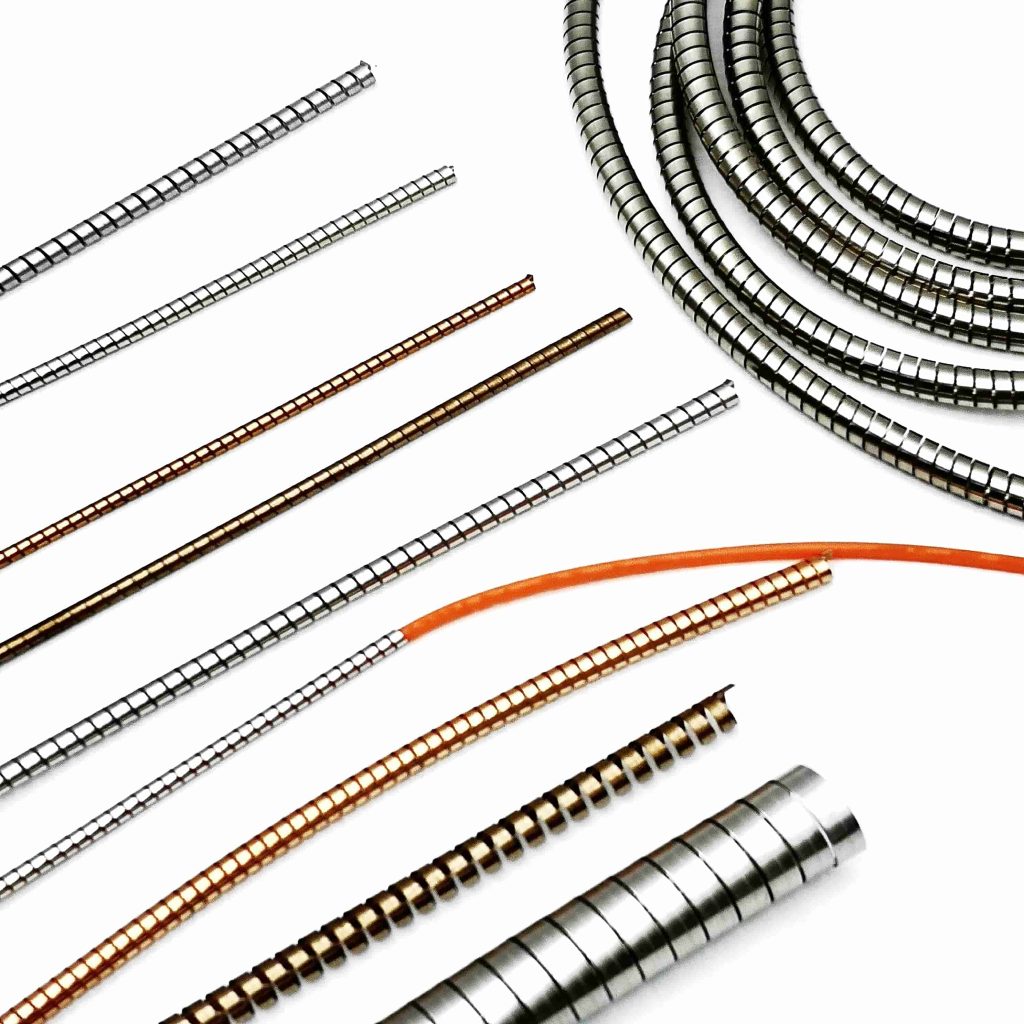
EMI Shielding Performance in Various Frequencies
The primary function of Handa spiral tubes is to block and attenuate electromagnetic interference across a broad frequency range. These tubes offer high levels of shielding in both high and low-frequency ranges, making them versatile for various industrial applications:
- High-Frequency Shielding:
- Range of 200 kHz to 10 GHz: Handa spiral tubes provide excellent shielding performance across this broad range, often achieving effectiveness levels of ≥90 dB. This makes them highly suitable for applications involving radar and communication systems.
- 1 GHz Performance: For many high-frequency applications, particularly in the telecommunications and aerospace industries, shielding effectiveness at or above 100 dB is a requirement. Handa spiral tubes typically exceed this threshold at 1 GHz, making them ideal for preventing interference in highly sensitive equipment.
- Low-Frequency Shielding:
- 10 kHz to 100 kHz Range: Even at lower frequencies, where effective shielding can be more challenging, Handa spiral tubes demonstrate effectiveness above 90 dB. This makes them valuable in power electronics and other applications requiring low-frequency shielding.
Performance in Humid and Corrosive Environments
One of the most notable advantages of Handa spiral tubes is their resilience in damp, saline, and corrosive conditions. This quality extends their range of application significantly, making them suitable for coastal and marine applications, as well as any setting where humidity is consistently high.
- Moisture and Corrosion Resistance:
- Enhanced Anti-Corrosion Capability: The combination of tin plating and edge coating protects Handa spiral tubes from moisture-induced corrosion. This feature is critical in applications that operate near bodies of water or in humid climates.
- Salt Spray Resistance: When exposed to salt spray or similar conditions, Handa spiral tubes maintain their integrity and shielding effectiveness, making them ideal for naval or coastal applications. The anti-corrosion properties extend the lifespan of the spiral tubes, reducing maintenance and replacement frequency.
- Long-Term Stability and Durability:
- Resistance to Environmental Aging: The high-quality materials used in Handa spiral tubes ensure that they resist aging and degradation, even under continuous exposure to high temperatures and humidity. This stability is crucial for applications where the tubes are expected to remain effective over long periods without frequent replacement.
- Consistent Shielding Effectiveness: Despite exposure to environmental challenges, Handa spiral tubes retain their EMI shielding capabilities over time, ensuring reliable performance for sensitive equipment in telecommunications, medical, and aerospace sectors.
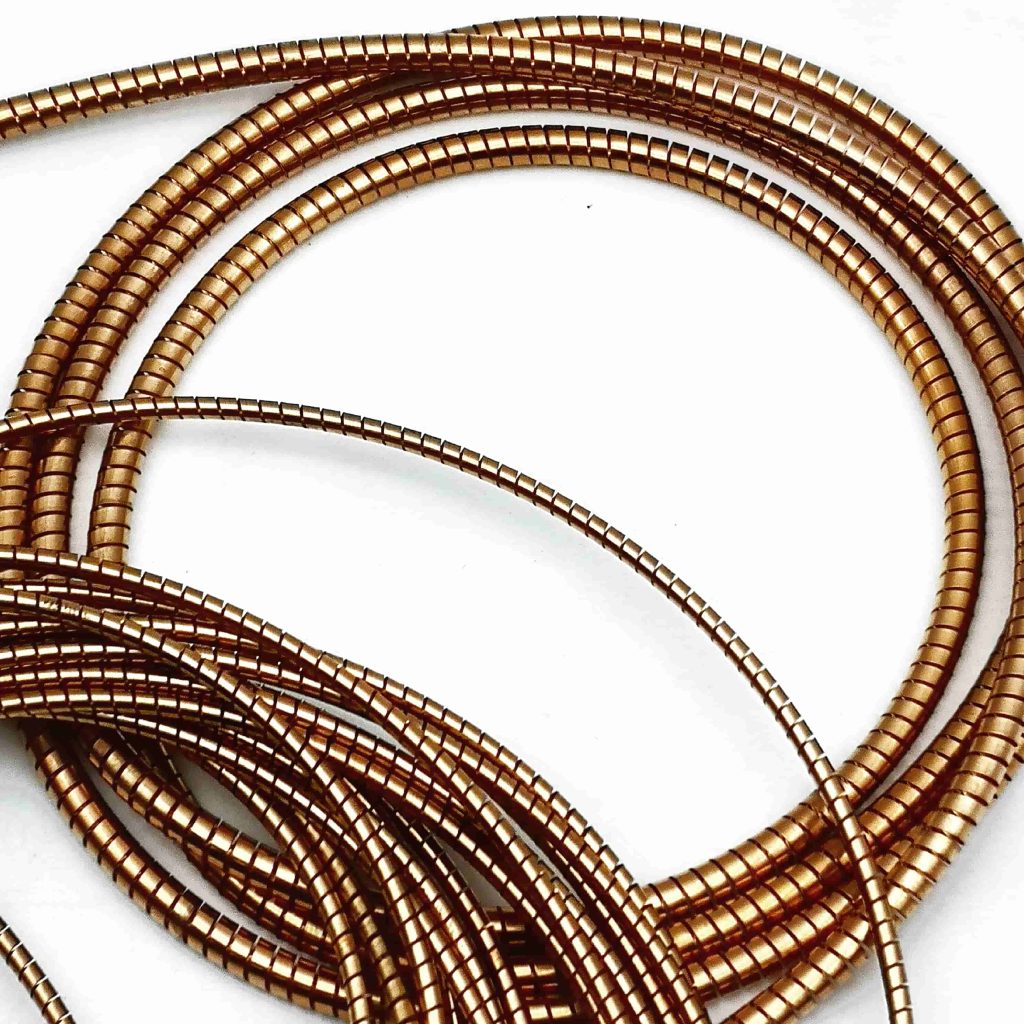
Applications Across Industries
Handa spiral tubes have applications in a range of sectors that require robust EMI shielding solutions, particularly where moisture or other challenging environmental factors are present.
- Military and Aerospace:
- Radar Systems: In radar equipment, Handa spiral tubes protect electronic systems from interference, allowing them to operate accurately in high-moisture environments, such as on naval vessels or coastal facilities.
- Navigation Systems: The spiral tubes are crucial for shielding sensitive components in navigation systems, providing reliability in environments that may expose equipment to salt and humidity.
- Telecommunications:
- Cellular and Satellite Base Stations: In telecommunications infrastructure, such as base stations and satellite ground stations, Handa spiral tubes ensure EMI shielding for essential components, especially in environments prone to high moisture levels.
- Satellite Communication Equipment: For satellite communication systems, effective EMI shielding is critical for maintaining signal purity. Handa spiral tubes help prevent signal interference and degradation in both terrestrial and extraterrestrial applications.
- Medical Equipment:
- MRI Machines: MRI machines require a shielded environment to prevent interference with imaging quality. Handa spiral tubes create this shielded environment, helping to block external electromagnetic fields, even in sterile and humid conditions.
- X-Ray Equipment: Handa spiral tubes protect the internal electronics in X-ray machines from interference and corrosion, ensuring consistent performance even in challenging environmental conditions.
- Precision Instrumentation:
- Measurement and Laboratory Equipment: Handa spiral tubes prevent EMI from affecting the accuracy of sensitive measurement equipment, a necessity in high-humidity environments like certain laboratory settings.
- Test Equipment: For high-precision instrumentation, the shielding properties of Handa spiral tubes contribute to accurate measurements by isolating equipment from external EMI sources.
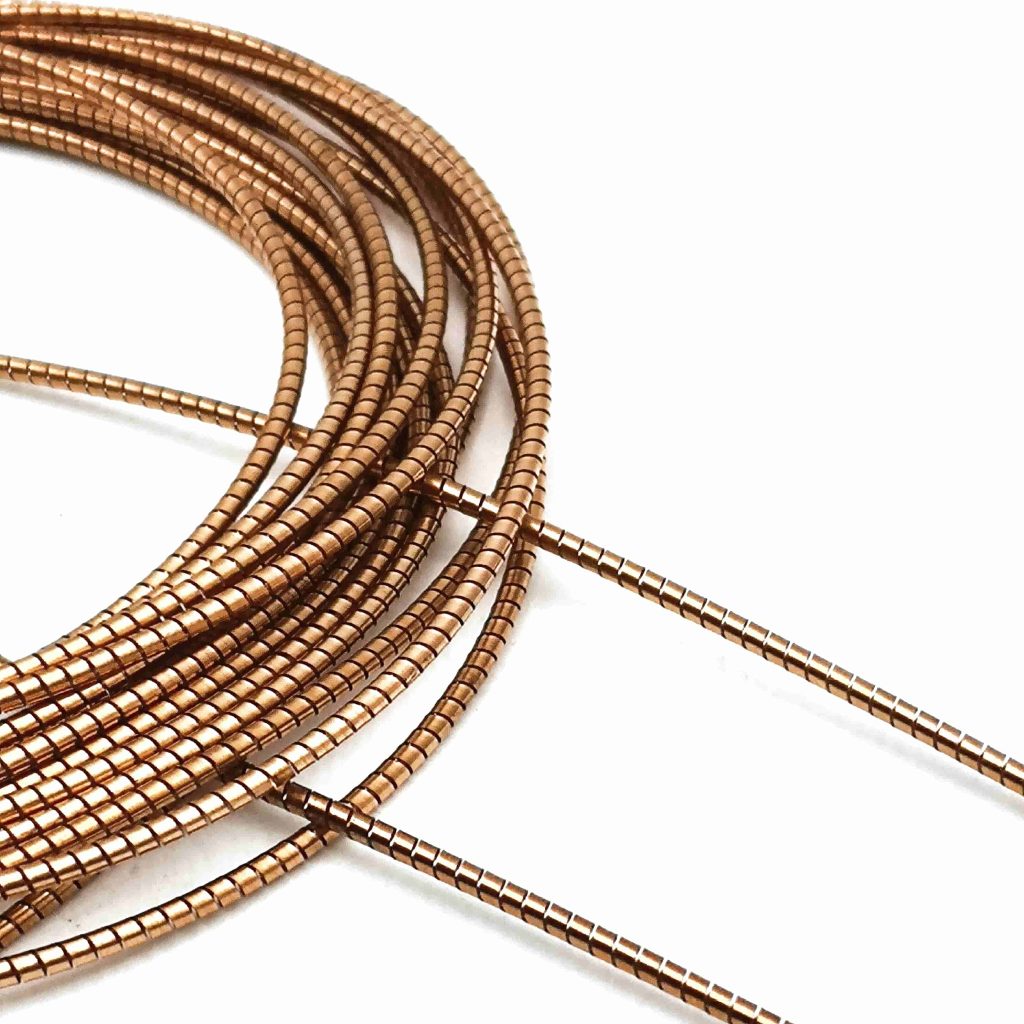
Installation and Maintenance Considerations
Effective installation and maintenance practices are essential to maximize the longevity and shielding performance of Handa spiral tubes.
- Avoid Over-Compression:
- Damage Prevention: Over-compression can lead to material deformation or damage, which reduces shielding effectiveness. Installation should be done according to manufacturer guidelines to ensure the proper compression ratio is maintained.
- Routine Inspection and Maintenance:
- Periodic Checks for Corrosion and Wear: Regular inspections help detect any signs of wear or damage early on. In environments where equipment is frequently assembled and disassembled, it is recommended to use tubes with high wear resistance, such as those with nickel or tin coatings.
- Material Selection for Longevity: In applications with frequent handling or environmental wear, materials with enhanced durability should be chosen to prevent early replacement.
- Optimized Storage Conditions:
- Humidity Control: To prevent premature corrosion, Handa spiral tubes should be stored in a dry, ventilated area, away from high-humidity conditions.
- Protection from Sulfur Compounds: Materials containing sulfur can accelerate the degradation of metals; thus, Handa spiral tubes should be stored in sulfur-free environments to maintain material integrity.
Conclusion and Future Outlook
The unique combination of durability, high conductivity, and resilience against corrosion makes Handa spiral tubes indispensable in EMI shielding applications, especially in challenging conditions like high humidity or saline exposure. The advanced material composition, coupled with precise surface treatments, ensures that these tubes maintain consistent shielding effectiveness across a wide frequency range.
Handa spiral tubes are particularly valuable in industries where electromagnetic interference can have significant consequences, such as in military, medical, and aerospace applications. In addition, their durability in moist environments makes them suitable for telecommunications and marine applications, where moisture and salt exposure are inevitable.
As technology advances, the demand for more sophisticated EMI shielding solutions will continue to grow. Handa spiral tubes are poised to meet this demand, thanks to their adaptability, robust material composition, and proven performance in high-demand settings. For optimal performance, it is advisable to work closely with manufacturers to customize spiral tubes to specific application requirements, taking into account factors like frequency range, environmental conditions, and desired lifespan. The future may also bring new materials and surface treatments that could further enhance the shielding capabilities of Handa spiral tubes, broadening their range of applications and effectiveness even further.
You May Also Like
-
EMI/EMC Shielding | RFI Shielding | EMI Gaskets
RF/EMI Shield Spiral Gasket
Spiral shielding gaskets are essential components in various industrial applications, providing electromagnetic interference (EMI) shielding while ensuring reliable sealing. Their effectiveness, however, can be compromised in corrosive environments, making it crucial to enhance their corrosion resistance. This article explores the multifaceted strategies employed to improve the corrosion resistance of spiral shielding gaskets, covering material selection, surface treatment, design optimization, environmental testing, the use of composite materials, and maintenance practices. By understanding these strategies, manufacturers can ensure the durability and reliability of spiral shielding gaskets in demanding conditions. 1. Material Selection2. Surface Treatment3. Design Optimization4. Environmental Adaptability Testing5. Composite Materials6. Maintenance and CareConclusion Spiral Shielding Gaskets providing electromagnetic interference (EMI) shielding 1. Material Selection The foundation of a gasket's performance lies in its material. For spiral shielding gaskets, the choice of material directly impacts their corrosion resistance. 1.1 Stainless Steel Alloys Stainless steel is the most commonly used material for spiral shielding gaskets due to its inherent corrosion resistance. Among the various grades, 316L stainless steel stands out for several reasons: Molybdenum Content: The addition of molybdenum enhances 316L's resistance to pitting and crevice corrosion, particularly in chloride-rich environments, which are common in many industrial applications. Low Carbon Content: The low......
-
EMI/EMC Shielding | RFI Shielding | EMI Gaskets
Fingerstrips
EMI Shielding Finger Stocks(Fingerstrips) Introduction to EMI Shielding Finger StocksBasic ConceptsKey Features and Types of EMI Shielding Finger StocksPerformance StandardsApplications of EMI Shielding Finger StocksInstallation MethodsAdvantages of EMI Shielding Finger StocksLimitations of EMI Shielding Finger StocksFuture DevelopmentsConclusion EMI Shielding Finger Stocks(Fingerstrips) are crucial components used in various industries to protect sensitive electronic equipment from electromagnetic interference (EMI). Made from specialized alloys such as beryllium copper, these materials ensure stable signal transmission while preventing external disturbances. This article will delve into the intricacies of EMI Shielding Finger Stocks, exploring their design, types, performance standards, applications, installation methods, advantages, limitations, and future developments. Introduction to EMI Shielding Finger Stocks Electromagnetic interference can significantly impact the performance and reliability of electronic devices. EMI Shielding Finger Stocks are engineered to mitigate these effects, providing a barrier that reflects or absorbs electromagnetic waves. Their unique design allows them to create effective seals in various electronic applications, ensuring that sensitive components remain protected from external interference. Basic Concepts EMI Shielding Finger Stocks consist of resilient metal strips with a "finger-like" structure. This design enhances the ability of the material to conform to irregular surfaces and create a reliable contact. Beryllium copper is often the material of......
-
EMI/EMC Shielding | RFI Shielding | EMI Gaskets
RF/EMI Shield Spiral Gasket
EMI (Electromagnetic Interference) shielding spiral tube gaskets are critical components in many electronic and industrial applications, designed to protect sensitive equipment from electromagnetic interference while also maintaining structural integrity in challenging environments. One of the primary concerns with these gaskets is their susceptibility to corrosion, which can compromise their effectiveness and longevity. This article explores strategies to enhance the corrosion resistance of EMI shielding spiral tube gaskets, focusing on material selection, surface treatments, design optimization, and maintenance practices. Understanding EMI Shielding Spiral Tube GasketsFunctionality and ImportanceComposite MaterialsAdvantages of Composite MaterialsMaintenance and CareInspectionImportance of Regular InspectionCleaningBenefits of Regular CleaningConclusion EMI Shielding Spiral Tube Gaskets Understanding EMI Shielding Spiral Tube Gaskets EMI shielding spiral tube gaskets are engineered to create a reliable seal between two surfaces, preventing electromagnetic waves from penetrating and interfering with the operation of electronic devices. They are typically made from conductive materials that offer both mechanical flexibility and electrical conductivity. However, the presence of moisture, chemicals, or extreme temperatures can lead to corrosion, undermining their effectiveness. Thus, enhancing corrosion resistance is essential for ensuring their longevity and performance. Functionality and Importance EMI shielding spiral tube gaskets serve multiple functions, including: Electromagnetic Shielding: They block unwanted electromagnetic radiation, preventing......
-
Shielding Gasket Solutions and Materials
Electrically conductive foam
Electrically conductive foam is an innovative material designed to combine the softness, flexibility, and compressibility of traditional foam with the ability to conduct electricity. This unique combination of properties makes conductive foam ideal for a variety of industries where both cushioning and electrical functionality are required, such as electronics, automotive, aerospace, medical devices, and military hardware. What is Electrically Conductive Foam?Key Characteristics of Electrically Conductive FoamApplications of Electrically Conductive FoamManufacturing Process of Electrically Conductive FoamAdvancements and Trends in Electrically Conductive FoamConclusion What is Electrically Conductive Foam? Electrically conductive foam is a specialized foam material that has been infused or coated with conductive materials such as carbon, silver, nickel, or copper. These conductive particles provide the foam with its unique ability to transmit electricity, allowing it to function as both a cushioning material and an electrically active component. The foam itself is typically made from polyurethane, polyethylene terephthalate (PET), or other flexible polymers, which provide the base mechanical properties such as compressibility, resilience, and environmental resistance. The conductive fillers are either mixed into the foam during production or applied as a surface coating, depending on the application’s requirements. Key Characteristics of Electrically Conductive Foam Electrically conductive foam offers several distinctive properties......
-
Handa Canted Coil Springs
Electrical conducting springs
conductive contact finger springs /conducting canted coil springs The Challenge of Maintaining Reliable ConductivityConductive Contact Finger Springs: A Reliable SolutionConsistent Force Across Wide Deflection RangeMultiple Contact Points for Reliable ConductivitySuperior Conductive PropertiesEfficient Heat ManagementEMI/RF Shielding CapabilitiesSupporting SWaP (Space, Weight, and Power) RequirementsLow Insertion Force for Delicate ApplicationsDurability in Challenging ConditionsCleanliness and Sterilization in Medical ApplicationsConclusion: The Versatility of Electrically Conductive Contact Finger Springs Electrically conductive contact finger springs are specialized components designed to serve as highly efficient electrical conductors in applications requiring robust electrical connections, even under challenging conditions such as vibration, dynamic loads, and mechanical shock. These finger springs are often used in various industrial, automotive, and high-tech environments where maintaining electrical integrity is crucial. This article will explore the advantages, applications, and technical considerations of electrically conductive contact finger springs, with an emphasis on their use in environments where consistent electrical conductivity is critical. The Challenge of Maintaining Reliable Conductivity In many industrial settings, maintaining a reliable electrical connection can be a significant challenge. Various operational conditions, such as vibration, mechanical shock, and dynamic loads, can make it difficult for traditional electrical connections to remain secure. For instance, in the petrochemical industry, downhole tools are exposed to extreme......