Spiral Shielding Gaskets providing electromagnetic interference (EMI) shielding
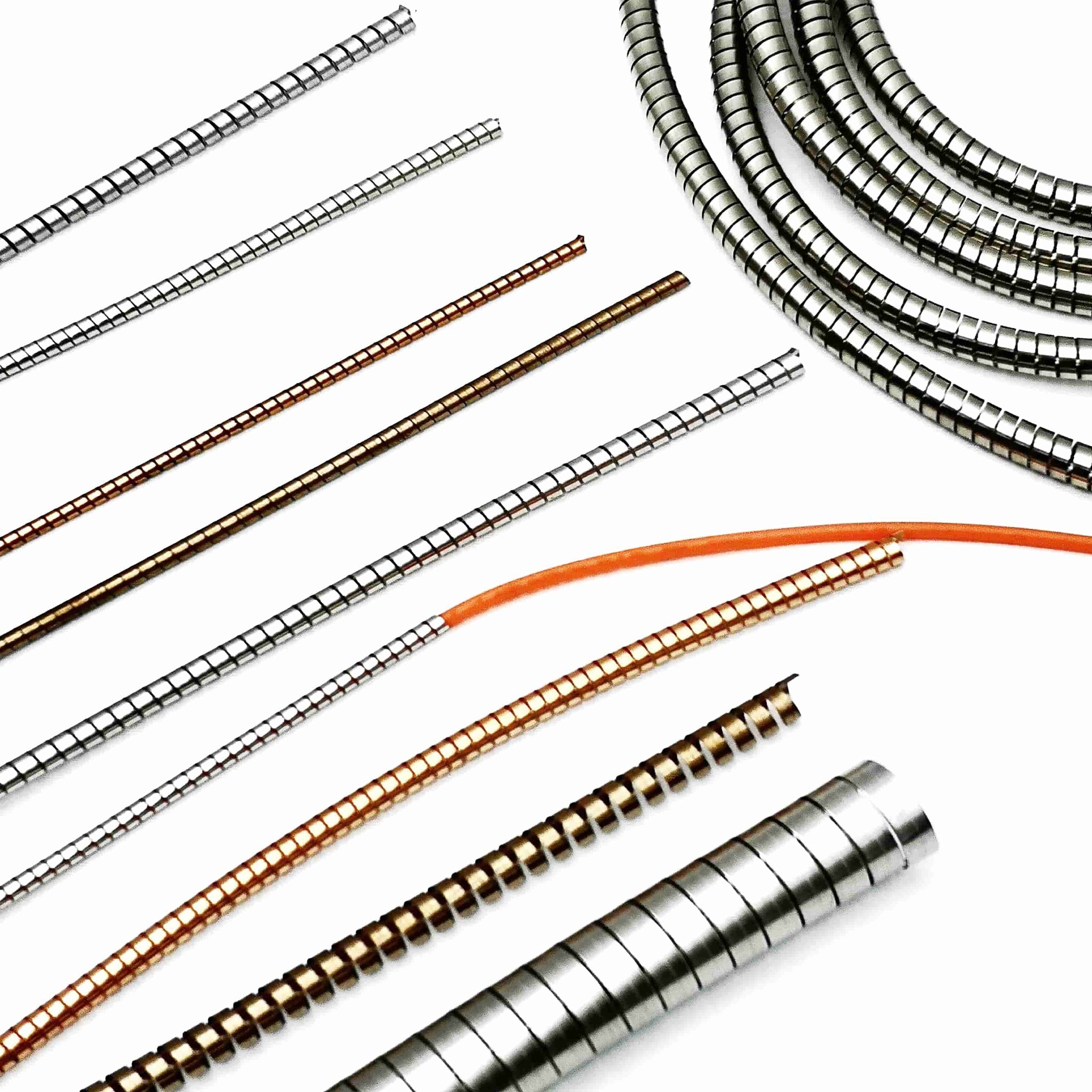
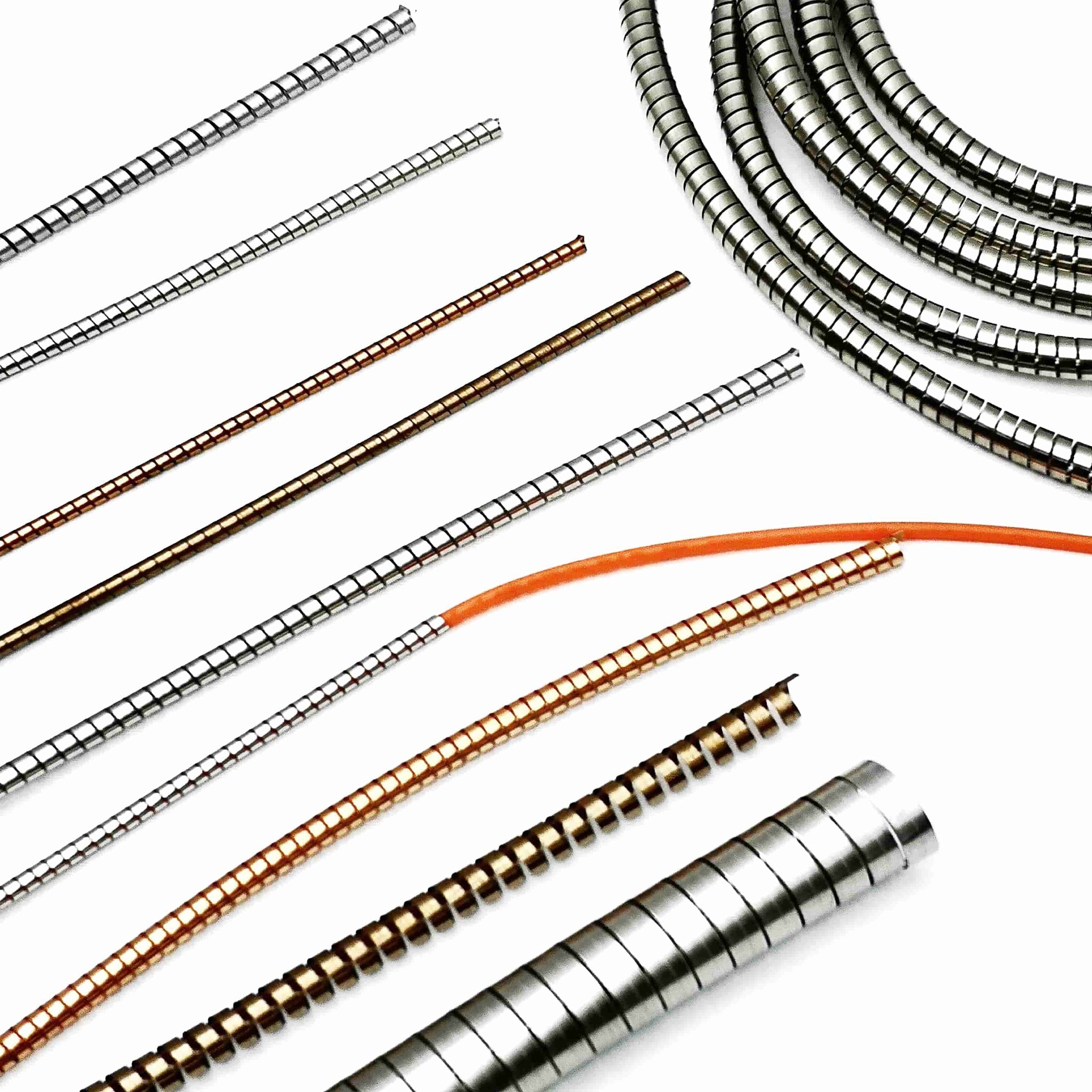
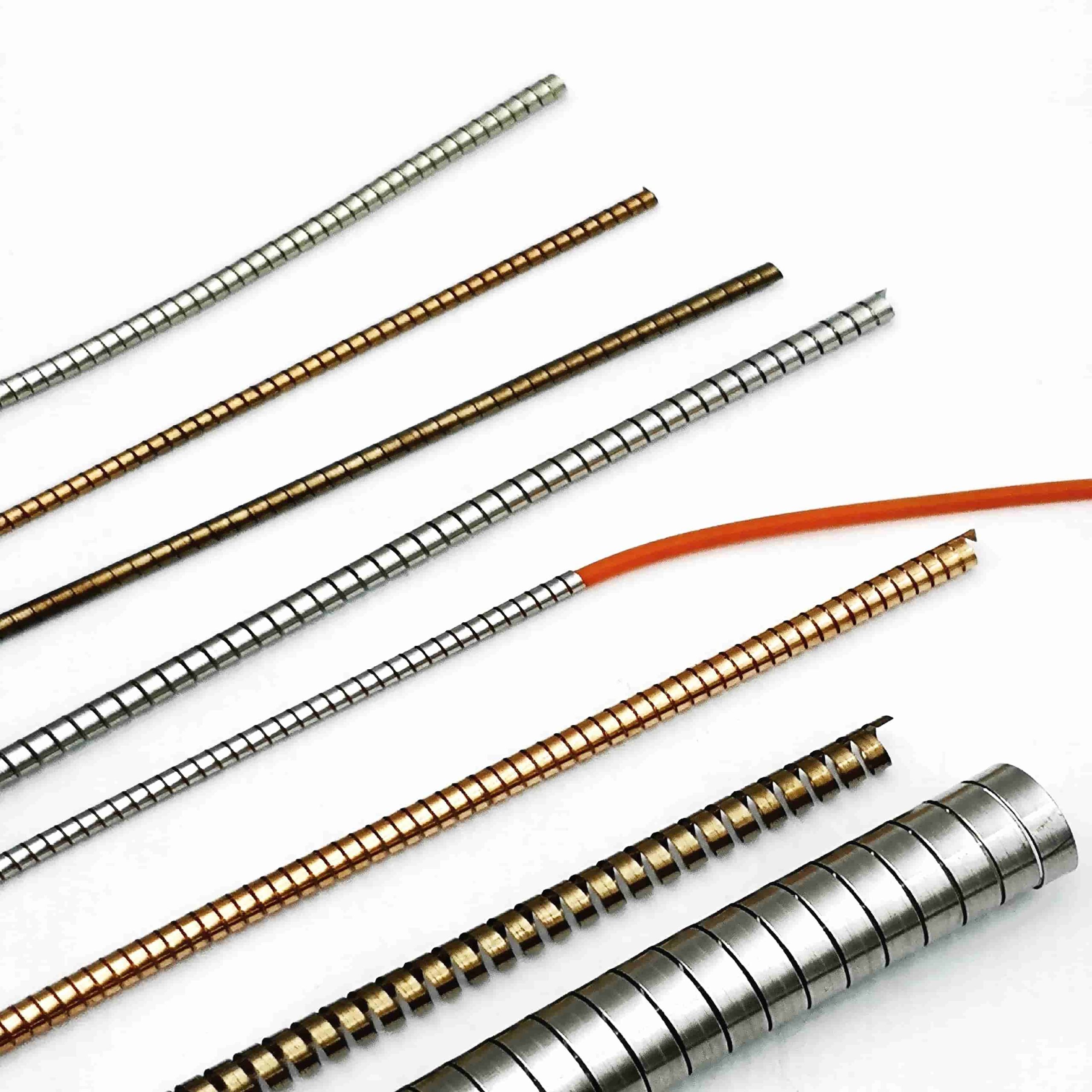
Spiral shielding gaskets are essential components in various industrial applications, providing electromagnetic interference (EMI) shielding while ensuring reliable sealing. Their effectiveness, however, can be compromised in corrosive environments, making it crucial to enhance their corrosion resistance.
Spiral shielding gaskets are essential components in various industrial applications, providing electromagnetic interference (EMI) shielding while ensuring reliable sealing. Their effectiveness, however, can be compromised in corrosive environments, making it crucial to enhance their corrosion resistance. This article explores the multifaceted strategies employed to improve the corrosion resistance of spiral shielding gaskets, covering material selection, surface treatment, design optimization, environmental testing, the use of composite materials, and maintenance practices. By understanding these strategies, manufacturers can ensure the durability and reliability of spiral shielding gaskets in demanding conditions.
Table of Contents
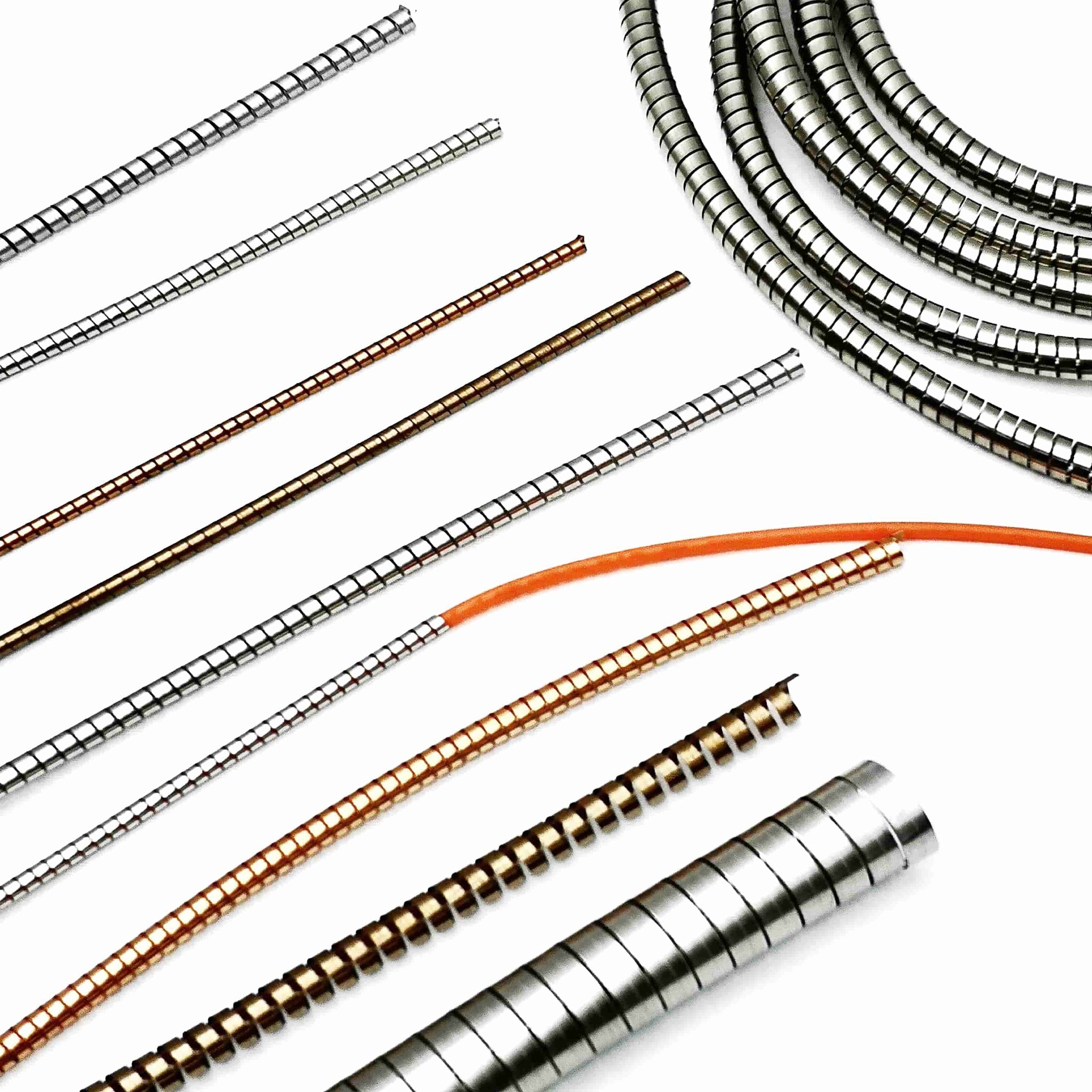
Spiral Shielding Gaskets providing electromagnetic interference (EMI) shielding
1. Material Selection
The foundation of a gasket’s performance lies in its material. For spiral shielding gaskets, the choice of material directly impacts their corrosion resistance.
1.1 Stainless Steel Alloys
Stainless steel is the most commonly used material for spiral shielding gaskets due to its inherent corrosion resistance. Among the various grades, 316L stainless steel stands out for several reasons:
- Molybdenum Content: The addition of molybdenum enhances 316L’s resistance to pitting and crevice corrosion, particularly in chloride-rich environments, which are common in many industrial applications.
- Low Carbon Content: The low carbon content of 316L minimizes carbide precipitation during welding, making it suitable for welded structures that may be exposed to corrosive media.
- High Strength: 316L stainless steel offers high strength and toughness, making it suitable for applications that require durability alongside corrosion resistance.
1.2 Alternative Alloys
In environments where 316L may not suffice, other high-corrosion-resistant alloys may be considered:
- Alloy 625: This nickel-based alloy has exceptional resistance to pitting and stress corrosion cracking, making it suitable for extreme environments, including chemical processing.
- Duplex Stainless Steels: These alloys combine austenitic and ferritic stainless steel properties, offering improved strength and resistance to corrosion.
2. Surface Treatment
Surface treatments can significantly enhance the corrosion resistance of spiral shielding gaskets. Various methods are employed to create protective barriers and improve surface characteristics.
2.1 Electroplating
Electroplating involves depositing a thin layer of metal onto the surface of the gasket. Common materials used for electroplating include nickel, chromium, and gold.
- Nickel Plating: This is one of the most popular electroplating methods for stainless steel gaskets. Nickel plating improves resistance to salt spray and other corrosive environments, extending the life of the gasket.
- Chrome and Gold Plating: While less common, these coatings can provide additional corrosion resistance and aesthetic appeal, particularly in consumer products.
2.2 Passivation
Passivation is a chemical treatment process that enhances the natural oxide layer on stainless steel surfaces. This process involves treating the steel with an acid solution, which removes free iron and other contaminants, leaving a more uniform and thicker oxide layer.
- Benefits: The passivated surface is more resistant to corrosion, as it minimizes the potential for localized corrosion that can occur in areas with disrupted oxide layers.
2.3 Coatings
Applying protective coatings to spiral shielding gaskets can provide an additional physical barrier against corrosive agents.
- Epoxy Coatings: These coatings are highly effective in preventing moisture ingress and protecting against chemical exposure.
- Polyurethane Coatings: Known for their flexibility and toughness, polyurethane coatings can absorb impacts and resist abrasions while providing a protective barrier.
- Fluoropolymer Coatings: These coatings offer excellent chemical resistance and are suitable for use in extreme temperature environments, providing long-lasting protection.
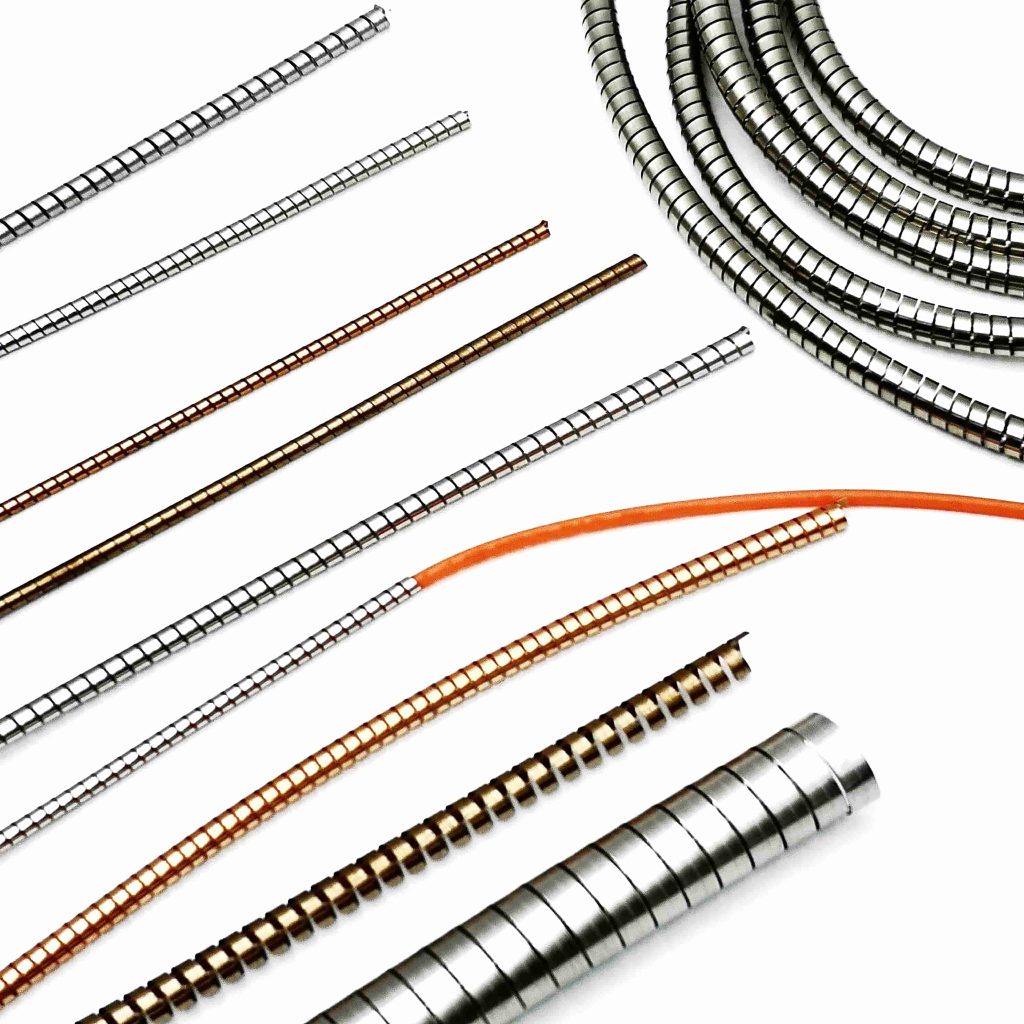
3. Design Optimization
Design plays a crucial role in the corrosion resistance of spiral shielding gaskets. By optimizing the design, manufacturers can minimize the potential for corrosion-related failures.
3.1 Sealing Design
A proper sealing design ensures that the gasket forms a tight seal with the mating surfaces, preventing moisture and corrosive agents from penetrating the system.
- Use of Sealing Rings: Integrating sealing rings or gaskets that conform well to the surfaces can enhance the overall sealing performance.
- Adhesives: Employing adhesives can also help to secure the gasket and prevent the ingress of moisture and corrosive materials.
3.2 Structural Design
The geometric design of spiral shielding gaskets can significantly influence their corrosion resistance.
- Stress Distribution: By designing the gasket to minimize stress concentrations, manufacturers can reduce the likelihood of corrosion-related failures. Areas of high stress are often the first to succumb to corrosion, so optimizing geometry can lead to increased durability.
- Thickness Variations: Careful consideration of the thickness of different sections of the gasket can also play a role. Thicker sections can provide greater resistance to mechanical wear and corrosion.
4. Environmental Adaptability Testing
To ensure that spiral shielding gaskets perform well under various environmental conditions, manufacturers must conduct thorough testing.
4.1 Salt Spray Testing
Salt spray testing is a standardized method for evaluating the corrosion resistance of materials in saline environments.
- Methodology: Gaskets are exposed to a saline mist for an extended period, and the degree of corrosion is assessed. This testing helps identify weaknesses in materials and coatings.
- Application: Results from salt spray tests can guide the selection of materials and coatings that will perform well in specific environments.
4.2 Humidity Testing
Humidity testing simulates conditions with high moisture content to assess the gasket’s performance in real-world scenarios.
- Importance: High humidity can accelerate corrosion processes, making it vital to evaluate how gaskets perform under these conditions.
- Testing Protocols: Testing typically involves subjecting the gaskets to controlled humidity levels for extended periods and then evaluating any signs of degradation or corrosion.
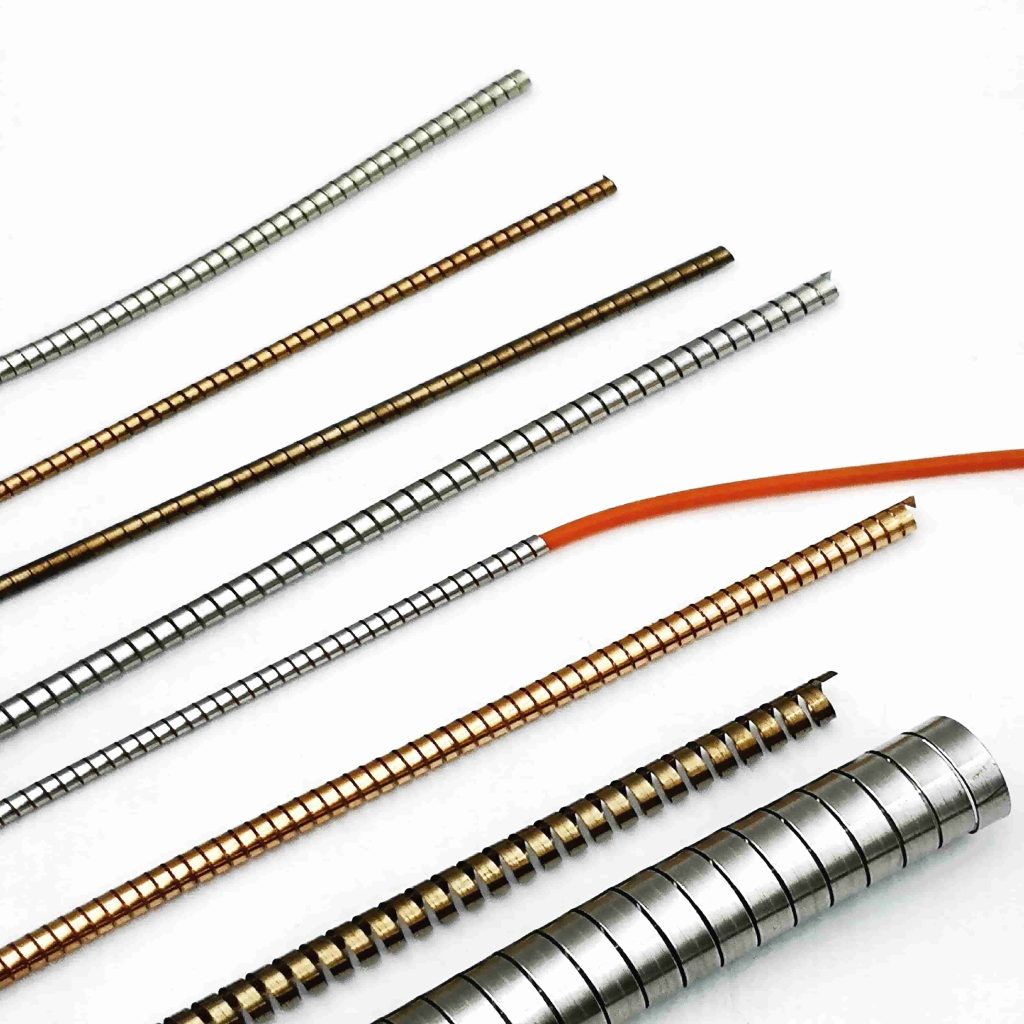
5. Composite Materials
In some applications, combining materials can yield improved performance characteristics, including corrosion resistance.
5.1 Use of Plastics and Ceramics
Integrating plastics or ceramics with stainless steel can enhance corrosion resistance and provide other beneficial properties.
- Plastic Liners: A plastic liner can create a non-corrosive barrier while the stainless steel provides structural integrity. This combination is especially useful in environments where chemical exposure is a concern.
- Ceramic Coatings: These can be applied to enhance wear resistance and protect against harsh chemicals, contributing to the overall durability of the gasket.
6. Maintenance and Care
Regular maintenance and care are essential for prolonging the life of spiral shielding gaskets and ensuring their effective performance.
6.1 Routine Inspections
Conducting regular inspections can help identify early signs of wear, corrosion, or degradation.
- Frequency: The frequency of inspections should depend on the operating environment and the criticality of the application. More rigorous environments may require more frequent checks.
- Documentation: Keeping a record of inspections can help track the performance of gaskets over time and identify any trends that may indicate potential issues.
6.2 Cleaning
Maintaining clean surfaces is vital for preventing localized corrosion and ensuring the effectiveness of protective coatings.
- Cleaning Procedures: Regularly removing dirt, debris, and corrosive residues helps maintain the integrity of the gasket’s surface and its protective coatings.
- Compatible Cleaners: It is essential to use cleaning agents that are compatible with the materials used in the gaskets to avoid unintentional damage.
6.3 Lubrication
In some applications, appropriate lubrication can enhance gasket performance and protect against corrosion.
- Selecting Lubricants: Using lubricants that are chemically compatible with the gasket materials is crucial. Incompatible lubricants can degrade the gasket and lead to premature failure.
- Benefits: Lubrication can reduce friction and wear, thus prolonging the life of dynamic seals in applications such as hydraulic systems.
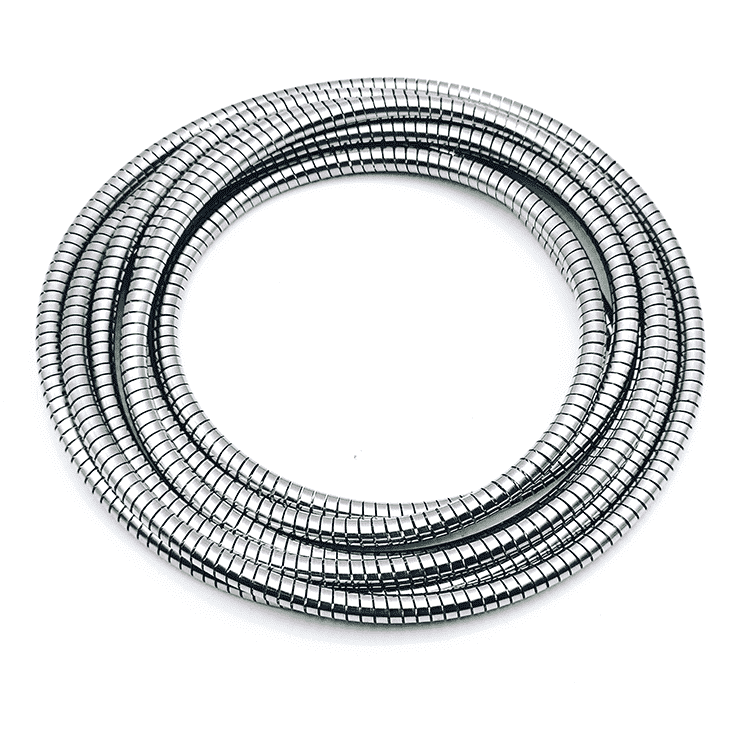
Conclusion
Enhancing the corrosion resistance of spiral shielding gaskets is critical for their performance in challenging environments. Through careful material selection, effective surface treatments, design optimization, thorough environmental testing, and diligent maintenance practices, manufacturers can significantly improve the durability and reliability of these vital components. As technology advances, ongoing research and development will continue to yield new materials and methods, further enhancing the efficacy of spiral shielding gaskets in a variety of industrial applications.
By integrating these strategies, spiral shielding gaskets can provide not only effective EMI shielding but also maintain structural integrity and long-term performance in the face of corrosive challenges. Ultimately, the enhanced corrosion resistance of these gaskets translates to increased equipment reliability, reduced maintenance costs, and prolonged service life, making them an invaluable asset in various industries.
You May Also Like
-
EMI/EMC Shielding | RFI Shielding | EMI Gaskets
Fingerstrips
EMI Shielding Finger Stocks(Fingerstrips) Introduction to EMI Shielding Finger StocksBasic ConceptsKey Features and Types of EMI Shielding Finger StocksPerformance StandardsApplications of EMI Shielding Finger StocksInstallation MethodsAdvantages of EMI Shielding Finger StocksLimitations of EMI Shielding Finger StocksFuture DevelopmentsConclusion EMI Shielding Finger Stocks(Fingerstrips) are crucial components used in various industries to protect sensitive electronic equipment from electromagnetic interference (EMI). Made from specialized alloys such as beryllium copper, these materials ensure stable signal transmission while preventing external disturbances. This article will delve into the intricacies of EMI Shielding Finger Stocks, exploring their design, types, performance standards, applications, installation methods, advantages, limitations, and future developments. Introduction to EMI Shielding Finger Stocks Electromagnetic interference can significantly impact the performance and reliability of electronic devices. EMI Shielding Finger Stocks are engineered to mitigate these effects, providing a barrier that reflects or absorbs electromagnetic waves. Their unique design allows them to create effective seals in various electronic applications, ensuring that sensitive components remain protected from external interference. Basic Concepts EMI Shielding Finger Stocks consist of resilient metal strips with a "finger-like" structure. This design enhances the ability of the material to conform to irregular surfaces and create a reliable contact. Beryllium copper is often the material of......
-
EMI/EMC Shielding | RFI Shielding | EMI Gaskets
RF/EMI Shield Spiral Gasket
EMI (Electromagnetic Interference) shielding spiral tube gaskets are critical components in many electronic and industrial applications, designed to protect sensitive equipment from electromagnetic interference while also maintaining structural integrity in challenging environments. One of the primary concerns with these gaskets is their susceptibility to corrosion, which can compromise their effectiveness and longevity. This article explores strategies to enhance the corrosion resistance of EMI shielding spiral tube gaskets, focusing on material selection, surface treatments, design optimization, and maintenance practices. Understanding EMI Shielding Spiral Tube GasketsFunctionality and ImportanceComposite MaterialsAdvantages of Composite MaterialsMaintenance and CareInspectionImportance of Regular InspectionCleaningBenefits of Regular CleaningConclusion EMI Shielding Spiral Tube Gaskets Understanding EMI Shielding Spiral Tube Gaskets EMI shielding spiral tube gaskets are engineered to create a reliable seal between two surfaces, preventing electromagnetic waves from penetrating and interfering with the operation of electronic devices. They are typically made from conductive materials that offer both mechanical flexibility and electrical conductivity. However, the presence of moisture, chemicals, or extreme temperatures can lead to corrosion, undermining their effectiveness. Thus, enhancing corrosion resistance is essential for ensuring their longevity and performance. Functionality and Importance EMI shielding spiral tube gaskets serve multiple functions, including: Electromagnetic Shielding: They block unwanted electromagnetic radiation, preventing......
-
Shielding Gasket Solutions and Materials
Electrically conductive foam
Electrically conductive foam is an innovative material designed to combine the softness, flexibility, and compressibility of traditional foam with the ability to conduct electricity. This unique combination of properties makes conductive foam ideal for a variety of industries where both cushioning and electrical functionality are required, such as electronics, automotive, aerospace, medical devices, and military hardware. What is Electrically Conductive Foam?Key Characteristics of Electrically Conductive FoamApplications of Electrically Conductive FoamManufacturing Process of Electrically Conductive FoamAdvancements and Trends in Electrically Conductive FoamConclusion What is Electrically Conductive Foam? Electrically conductive foam is a specialized foam material that has been infused or coated with conductive materials such as carbon, silver, nickel, or copper. These conductive particles provide the foam with its unique ability to transmit electricity, allowing it to function as both a cushioning material and an electrically active component. The foam itself is typically made from polyurethane, polyethylene terephthalate (PET), or other flexible polymers, which provide the base mechanical properties such as compressibility, resilience, and environmental resistance. The conductive fillers are either mixed into the foam during production or applied as a surface coating, depending on the application’s requirements. Key Characteristics of Electrically Conductive Foam Electrically conductive foam offers several distinctive properties......
-
Handa Canted Coil Springs
Electrical conducting springs
conductive contact finger springs /conducting canted coil springs The Challenge of Maintaining Reliable ConductivityConductive Contact Finger Springs: A Reliable SolutionConsistent Force Across Wide Deflection RangeMultiple Contact Points for Reliable ConductivitySuperior Conductive PropertiesEfficient Heat ManagementEMI/RF Shielding CapabilitiesSupporting SWaP (Space, Weight, and Power) RequirementsLow Insertion Force for Delicate ApplicationsDurability in Challenging ConditionsCleanliness and Sterilization in Medical ApplicationsConclusion: The Versatility of Electrically Conductive Contact Finger Springs Electrically conductive contact finger springs are specialized components designed to serve as highly efficient electrical conductors in applications requiring robust electrical connections, even under challenging conditions such as vibration, dynamic loads, and mechanical shock. These finger springs are often used in various industrial, automotive, and high-tech environments where maintaining electrical integrity is crucial. This article will explore the advantages, applications, and technical considerations of electrically conductive contact finger springs, with an emphasis on their use in environments where consistent electrical conductivity is critical. The Challenge of Maintaining Reliable Conductivity In many industrial settings, maintaining a reliable electrical connection can be a significant challenge. Various operational conditions, such as vibration, mechanical shock, and dynamic loads, can make it difficult for traditional electrical connections to remain secure. For instance, in the petrochemical industry, downhole tools are exposed to extreme......
-
Fingerstrips
Beryllium-copper fingerstrips series
https://www.handashielding.com/contact-us.html Handa Beryllium-Copper Fingerstrips/Fingerstocks with a variety of benefits Introduction to Handa Beryllium-Copper Fingerstrips/FingerstocksOverview of Beryllium-Copper as a MaterialKey Features of Handa Beryllium-Copper Fingerstrips/FingerstocksApplications of Handa Beryllium-Copper Fingerstrips/FingerstocksAdvantages of Using Handa Beryllium-Copper Fingerstrips/FingerstocksInstallation and Best PracticesConclusion Introduction to Handa Beryllium-Copper Fingerstrips/Fingerstocks Handa beryllium-copper fingerstrips, also known as fingerstocks, are highly efficient EMI (Electromagnetic Interference) shielding components. These products are essential in various industries, where sensitive electronic equipment requires protection from external electromagnetic and radio frequency interference (RFI). Beryllium-copper is a popular material for this purpose due to its outstanding combination of mechanical strength, electrical conductivity, and durability. As electronic devices become smaller and more integrated, the demand for highly effective shielding materials has increased. Handa beryllium-copper fingerstrips/fingerstocks provide a versatile solution for shielding gaps, seams, and other openings where electromagnetic radiation can escape or penetrate. This article will explore the design, features, applications, and benefits of these specialized shielding components. Overview of Beryllium-Copper as a Material Before diving into the specifics of Handa's fingerstrips, it is crucial to understand the material used—beryllium copper. Beryllium copper is a copper alloy with small amounts of beryllium (typically 0.5% to 3%). This combination offers several advantages: High Conductivity: Copper is known for its......