Do You Know Handa EMI Shielding Stainless Steel Spiral Tube Gaskets?
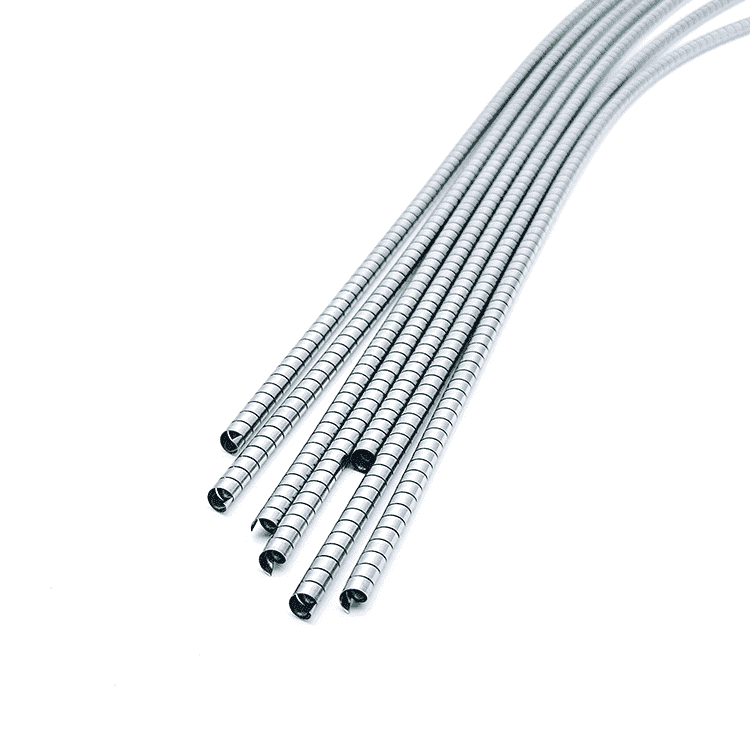
Handa EMI Shielding Stainless Steel
Spiral Tube Gaskets
Table of Contents
Handa EMI shielding stainless steel spiral tube gaskets,also known as Handa Quick Shield,are an advanced and versatile solution for electromagnetic interference (EMI) shielding and mechanical sealing across various industries. With unique design features and superior material properties, these components have revolutionized how engineers approach EMI mitigation and environmental sealing challenges.
1. Introduction to Stainless Steel Spiral Tube Gaskets
1.1 Definition and Purpose
Stainless steel spiral tube gaskets are cylindrical, spring-like components designed to block EMI and provide reliable mechanical sealing. Their inherent flexibility and high-performance materials make them an indispensable choice for applications requiring robust and adaptable shielding solutions.
1.2 Structure and Composition
The unique spiral design enhances compression uniformity, allowing for optimal contact with mating surfaces. Stainless steel spiral tube gaskets are typically manufactured from stainless steel grades such as SS301, SS304, and SS316, or conductive alloys like beryllium copper. They can also be plated with materials like tin or nickel to enhance conductivity and environmental resistance.
1.3 Role in Modern Engineering
As electronic systems become more complex and compact, the need for effective EMI shielding grows. Stainless steel spiral tube gaskets provide the perfect balance of mechanical durability, adaptability, and high shielding effectiveness, making them a cornerstone in modern EMI management.
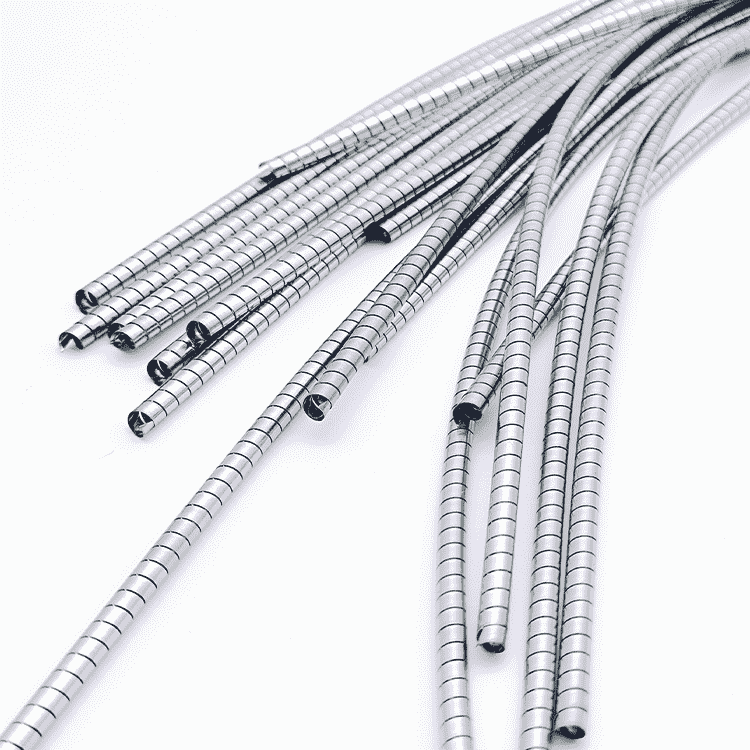
2. Key Features and Advantages
2.1 Superior EMI Shielding Performance
- Electromagnetic Wave Reflection and Absorption: Stainless steel exhibits excellent electrical conductivity, allowing it to reflect and absorb electromagnetic waves effectively.
- Multi-Layer Shielding Design: Advanced designs often incorporate multiple conductive layers, significantly enhancing shielding efficiency at high frequencies.
- Reliable Shielding Across Frequencies: These gaskets achieve shielding effectiveness exceeding 95 dB at 1 GHz, ensuring robust protection against EMI across a broad spectrum.
2.2 Mechanical Strength and Durability
- Elasticity: Their spiral structure ensures excellent resilience, enabling them to maintain consistent compression and contact even after repeated use.
- Resistance to Wear and Fatigue: High-grade materials like SS316 provide superior durability, making these gaskets ideal for applications with frequent dynamic loads.
- Adaptability to Vibration and Pressure: The gaskets’ mechanical robustness ensures stability and performance under challenging conditions, such as high-vibration environments.
2.3 Corrosion and Environmental Resistance
- Stainless Steel Benefits: Resistant to rust, moisture, and saline environments, stainless steel ensures long-term durability.
- Protective Coatings: Tin or nickel plating enhances corrosion resistance, conductivity, and wear resistance, making stainless steel spiral tube gaskets suitable for harsh conditions.
2.4 Customization and Versatility
- Design Flexibility: The gaskets can be customized to fit specific dimensions, shapes, and application requirements.
- Ease of Integration: Their spiral construction allows easy insertion into grooves and tight spaces, accommodating irregular surfaces and complex geometries.
- Adaptable to Varied Applications: Whether in aerospace or consumer electronics, stainless steel spiral tube gaskets deliver consistent performance across different environments.
2.5 Cost Efficiency
- High Value for Performance: Stainless steel spiral tube gaskets offer an excellent cost-to-performance ratio, outperforming many alternative shielding solutions.
- Low Maintenance Requirements: Their durability and resistance to environmental degradation reduce long-term operational costs.
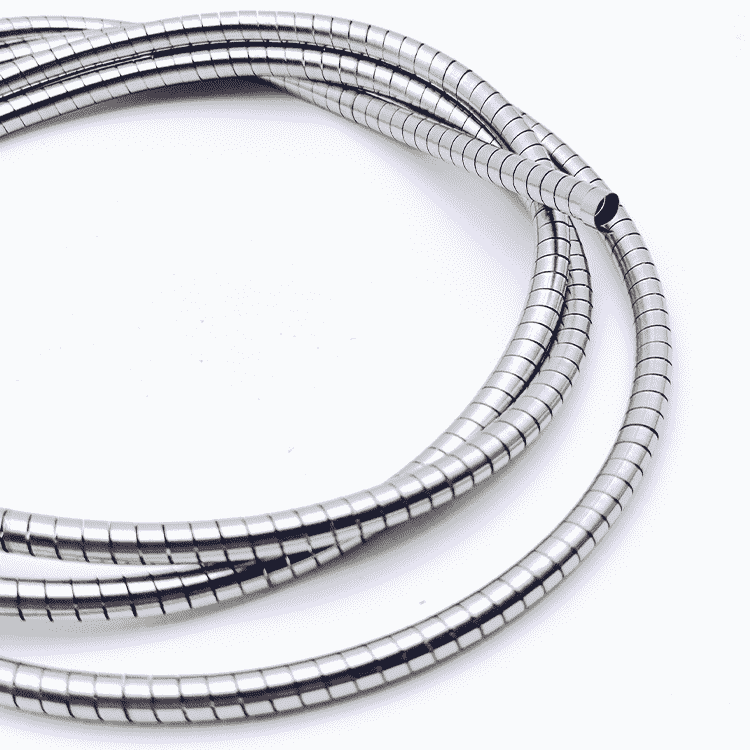
3. Applications Across Diverse Industries
Stainless steel spiral tube gaskets are indispensable in a variety of industries due to their adaptability and high performance:
3.1 Telecommunications
- Shield antennas, RF modules, and cellular base stations from EMI, ensuring stable and clear signal transmission.
- Protect 5G and satellite communication systems, where signal integrity is critical.
3.2 Semiconductor Manufacturing
- Provide EMI shielding for wafer fabrication equipment, preventing malfunctions caused by electromagnetic disturbances.
- Enhance the precision of semiconductor testers and packaging systems, ensuring reliable results in controlled environments.
3.3 Medical Devices
- Ensure the accuracy of imaging devices such as MRI and CT scanners by blocking external EMI.
- Protect sensitive monitoring equipment, like electrocardiograms (ECGs), ensuring data accuracy and patient safety.
3.4 Aerospace and Defense
- Safeguard avionics systems, communication equipment, and radar technologies in high-stress environments.
- Enhance the reliability of military-grade devices, such as secure communication and navigation systems.
3.5 Automotive Electronics
- Shield vehicle sensors, electronic control modules, and infotainment systems, ensuring reliable operation in diverse driving conditions.
- Improve the performance and safety of electric vehicles (EVs) by protecting battery systems and power electronics from interference.
3.6 Consumer Electronics
- Enhance signal quality in devices such as smartphones, laptops, and wearables.
- Protect IoT devices and smart appliances, ensuring consistent performance in connected environments.
3.7 Industrial Machinery
- Maintain operational reliability in machinery control systems, robotics, and automation equipment.
- Protect electronic components in harsh industrial settings, such as factories and chemical plants.
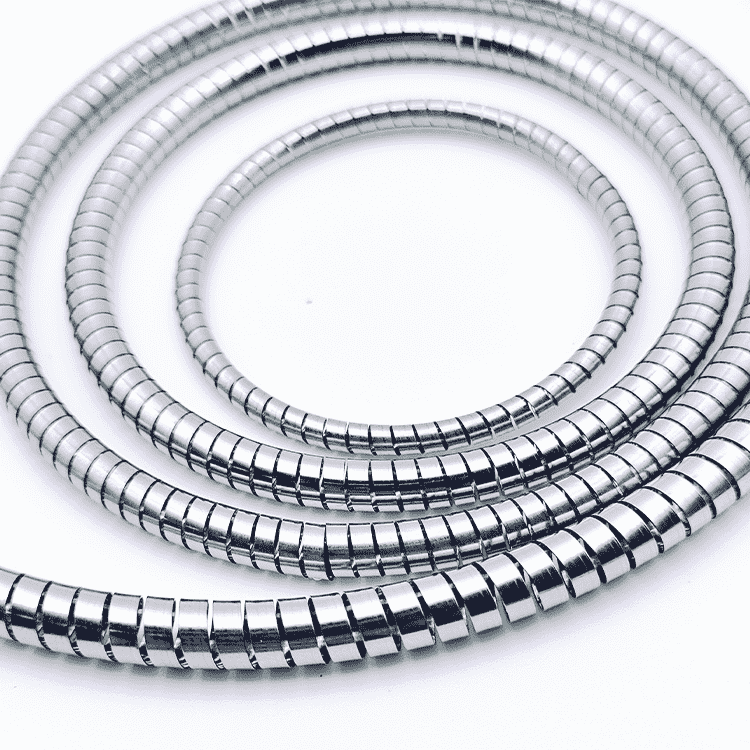
4. Material and Coating Options
4.1 Stainless Steel Grades
- SS301: Offers excellent formability and moderate strength, suitable for standard applications.
- SS304: Combines high corrosion resistance with good mechanical performance.
- SS316: Provides enhanced resistance to extreme environments, including chemical exposure and marine conditions.
4.2 Conductive Alloys
- Beryllium Copper: Known for its exceptional elasticity and electrical conductivity, making it ideal for precision applications.
4.3 Coating Options
- Tin Plating: Improves conductivity and provides superior resistance to humid environments.
- Nickel Plating: Offers excellent wear resistance and stability in high-temperature settings.
5. Environmental Adaptability
5.1 Temperature Resistance
- Perform reliably across a wide temperature range, from cryogenic conditions to high-heat industrial environments.
- Stainless steel grades like SS316 maintain performance even at temperatures exceeding 300°C.
5.2 Resistance to Corrosion and Moisture
- Withstand exposure to saline, humid, and chemically aggressive environments, ensuring long-term stability.
- Plated options provide additional protection against electrochemical corrosion in challenging settings.
5.3 Adaptation to Dynamic Environments
- Resilient under vibration, compression, and dynamic mechanical loads, making them suitable for high-motion applications.
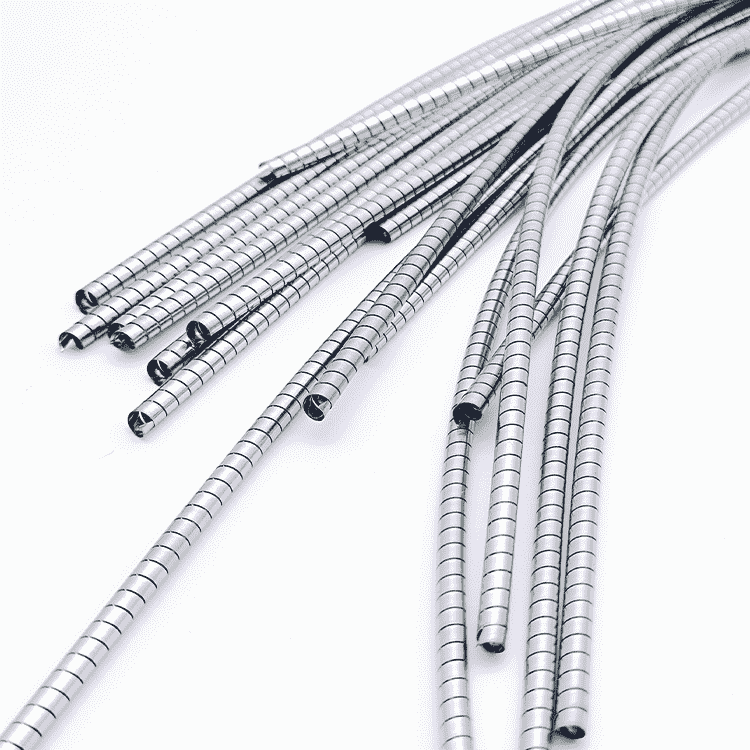
6. Standards and Testing
To ensure high performance and reliability, stainless steel spiral tube gaskets are subjected to rigorous testing:
- EMI Shielding Effectiveness: Tested for decibel attenuation across frequency ranges to meet industry benchmarks.
- Mechanical Properties: Compression, fatigue resistance, and resilience tests confirm their durability.
- Environmental Resistance: Simulated exposure to humidity, temperature extremes, and corrosive environments validates their longevity.
7. Future Trends and Innovations
7.1 Advanced Material Integration
Emerging materials like graphene composites and carbon nanotubes may enhance the performance of spiral tube gaskets by improving conductivity and reducing weight.
7.2 Miniaturization for Compact Devices
With the rise of compact electronic devices, the demand for thinner, more flexible gaskets that maintain high performance is increasing.
7.3 Smart Technology Integration
Integrating sensors into gaskets to monitor real-time conditions like compression, temperature, and wear could revolutionize predictive maintenance and operational efficiency.
7.4 Sustainable Manufacturing
Future designs will focus on recyclable materials and energy-efficient production processes to align with global sustainability goals.
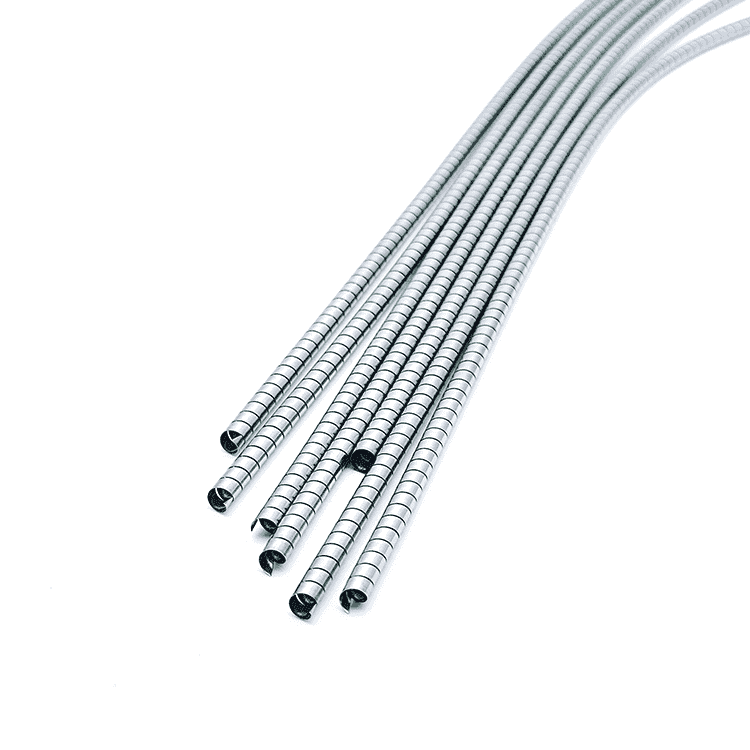
8. Guidelines for Selection
When choosing stainless steel spiral tube gaskets, consider the following:
- Application Environment: Assess factors such as temperature, humidity, and chemical exposure.
- Performance Requirements: Determine shielding effectiveness, mechanical strength, and durability needs.
- Customization Needs: Opt for tailored solutions for unique shapes, sizes, or specific industry requirements.
Conclusion
Stainless steel spiral tube gaskets represent the pinnacle of EMI shielding and mechanical sealing technology. Their superior performance, adaptability, and cost efficiency make them indispensable across a broad spectrum of industries, including telecommunications, aerospace, automotive, and medical technology. As advancements in materials and manufacturing techniques continue, these gaskets are poised to meet the ever-increasing demands of modern engineering, ensuring reliable and efficient performance in a rapidly evolving technological landscape.
For more information about specific products and configurations, explore trusted sources like Handa Shielding.